- All Categories

-
Ophir by MKS
Ophir Power/Energy Meter Calibration Procedure
When it comes to laser measurement systems, accuracy is super important. A world-leader like Ophir uses strict processes to ensure measurement accuracy and analyze – and ...
02:37Ophir Power/Energy Meter Calibration ProcedureWhen it comes to laser measurement systems, accuracy is super important. A world-leader like Ophir uses strict processes to ensure measurement accuracy and analyze – and quantify - calibration errors. Let’s look at Ophir’s article and see how they’re making sure their laser power and energy meters meet specifications.
The total accuracy of measurement is influenced by many different factors – such as wavelength, sensor linearity, uniformity of readings over the surface, pulse rate, display unit calibration uncertainty, damage done to the absorber surface, and electromagnetic interference. The article describes all of these factors, and how they are handled when it comes to Ophir sensors – read the article in full to find out more.
The article primarily discusses two factors – firstly – the power calibration uncertainty of the measuring sensor at the power level, energy level, and wavelength at which it was calibrated, and secondly - the energy calibration uncertainty – this is the extra error due to the extra calibration step needed to calibrate energy.
Ophir’s accuracy specifications are in general “2 Sigma”. This means that, statistically, in 95% of cases the error of the system measured will not exceed the stated error. For example, if the stated error is plus minus 3 percent, then in 95% of cases, it will not exceed 3%, and in 99% of cases, it will not exceed 4%.
Ophir goes to great lengths to ensure sensors are calibrated to meet strict requirements. The possible errors are analyzed using advanced statistical techniques, resulting in highly accurate and reliable specifications. This is done for all types of sensors, and the article outlines the exact calculations made, as well as the resulting expected error, for each type of Ophir measurement device.
If you’re interested in knowing all of the hard work that goes into ensuring that Ophir’s high quality laser measurement devices have accurate specifications and minimal total error, be sure to check out the article.
We just need your phone...After entering the number, the mobile send button will be available to you in all items.
Send to mobileAfter a short one-time registration, all the articles will be opened to you and we will be able to send you the content directly to the mobile (SMS) with a click.We sent you!The option to cancel sending by email and mobile Will be available in the sent email.00:0002:37
60% CompleteSoon... -
Ophir by MKS
So you want to convert a laser wavelength?
The wavelength of a laser is one of its fundamental characteristics. Laser diodes, one of the most common laser sources, have wavelengths determined by their design and the ...
03:22So you want to convert a laser wavelength?The wavelength of a laser is one of its fundamental characteristics. Laser diodes, one of the most common laser sources, have wavelengths determined by their design and the materials they are made from. But what happens when you need a specific wavelength for your application, and the laser can’t generate it? That’s where laser wavelength conversion is used. Let’s take a look at Ophir’s article and find out how this is done.
First, let’s talk about tuneable lasers. Some lasers can be tuned, although the tuning range is limited by the gain medium bandwidth. The tuning is done by controlling loss in the laser cavity so it’s minimized for the wavelength at which lasing occurs. Tuning mechanisms can include controlling the laser’s temperature, or using microelectromechanical actuators to change the cavity’s length.
Most solid state lasers are not tuneable, as they have a narrow gain spectrum. One exception is the Ti-Sapphire laser which has a wide gain bandwidth and can be tuned between 650-1100 nanometers.
Linear wavelength conversion involves using the laser to pump a gain medium, such as a crystal, to a higher energy state – and the excited electrons then decay to a lower energy state by emitting radiation at a longer wavelength. Put the gain medium in a cavity, and a laser is formed. An example is the Nd-YAG laser, which is pumped by a laser diode at 808 nanometers and emits radiation at 1064 nanometers.
Next, we have nonlinear wavelength conversion, such as second-harmonic generation (SHG). A well-known example is the green laser that that uses a nonlinear crystal to convert 1064 nanometers to 532 nanometers. There are many requirements involved in this type of conversion, such as meeting phase matching conditions – read the article to find out more.
Lastly, we have non-coherent laser-driven light sources. One example is the generation of plasma that emits extreme ultraviolet radiation at a wavelength of 13 nanometers. This plasma is generated by focusing a high power CO2 laser, with a wavelength of about 10 micrometers, onto tin droplets in a vacuum – resulting in EUV light that enables advanced photolithography in the microelectronics industry. Read more about it in the article.
So, to round it up – it’s not always possible to get the wavelength you need for a specific application, due to limitations in the laser and in the materials and processes involved. But, nonlinear optical elements can allow the laser industry to reach further into more wavelength regions, enabling processes that are otherwise impossible to attain.
We just need your phone...After entering the number, the mobile send button will be available to you in all items.
Send to mobileAfter a short one-time registration, all the articles will be opened to you and we will be able to send you the content directly to the mobile (SMS) with a click.We sent you!The option to cancel sending by email and mobile Will be available in the sent email.00:0003:22
60% CompleteSoon... -
Ophir by MKS
Measurement tools? Lasers are leading the way
Lasers are used in so many ways, from optical fiber internet to performing sophisticated medical procedures. But they’re also superstars in another field – measurements...
03:12Measurement tools? Lasers are leading the wayLasers are used in so many ways, from optical fiber internet to performing sophisticated medical procedures. But they’re also superstars in another field – measurements. Let’s explore Ophir’s article on lasers as measurement tools.
Laser-assisted measurements can enhance and improve the way physical quantities are measured. They can calculate the distance between objects, using different methods depending on the size of the object, it’s distance from the measurement device, and the required resolution.
For example, there’s LiDAR – which encompasses a range of techniques for generating 3D maps of the environment, based on projecting laser light and detecting the reflected signal. It’s often used for autonomous vehicle navigation, to determine the best and safest driving strategy.
Lasers have been useful in other fields of measurement – such as interferometry, spectroscopy, microscopy, and atomic clocks.
Interferometry relies on superimposing electromagnetic radiation that has traversed different optical paths, and extracting information from the resulting interference pattern. The world’s most advanced interferometer stands in the heart of the Laser Interferometer Gravitational-Wave Observatory experiment. It can detect gravitational waves due to the change they exert on a laser beam that travels in one of its four-kilometer-long interferometer arms, measuring changes in optical path of less than one ten thousandth of the size of a proton! Read the article to find out more.
Spectroscopy is the study of interaction between light and matter – a laser with a well-defined wavelength can be used to investigate energy gaps between two electronic states of atoms or molecules. This technology has allowed scientists to catalog atomic and molecular transitions of almost every element and molecule known to us.
Microscopy is the use of microscopes to magnify objects. At first, microscopes used only lenses to view the object with visible light, and their maximum resolution was limited by diffraction due to the wave nature of light. But super-resolution microscopes, using lasers, have found ways to surpass the diffraction limit, with incredible results.
Lastly – lasers play a key role in atomic clocks – the most precise time-measurement system device built by man. Atomic clocks use the known energy-level differences of certain atoms to generate a highly stable and repeatable signal, with a known frequency - from which time can be measured. Read the article to find out more about the laser’s involvement in this fascinating application.
All in all, lasers have contributed greatly to developing measurement tools that go above and beyond the capabilities of other measurement technologies.
We just need your phone...After entering the number, the mobile send button will be available to you in all items.
Send to mobileAfter a short one-time registration, all the articles will be opened to you and we will be able to send you the content directly to the mobile (SMS) with a click.We sent you!The option to cancel sending by email and mobile Will be available in the sent email.00:0003:12
60% CompleteSoon... -
Ophir by MKS
A journey through the evolution of man-made light sources
Since the beginning of time, man had busied itself with creating light sources. Let’s travel through time using Ophir’s article to explore the man-made light sources of...
03:03A journey through the evolution of man-made light sourcesSince the beginning of time, man had busied itself with creating light sources. Let’s travel through time using Ophir’s article to explore the man-made light sources of the past, present, and future.
The earliest light sources were of course fire-based. The humble fire served as a light source, but also provided heat for cooking and warmth. Then, candles and oil lamps allowed fire to be controlled just for the purpose of providing light.
Moving on to the beginning of the 19th century, gas lanterns appeared in the streets of major European and American cities.
At the end of the 19th century, the incandescent light bulb made its first appearance – the rise of the electric light. 140 years later, we still use these bulbs. However, there are some problems – with electric current transmitting through a highly-resistant filament, only a very small portion of electrical energy is made into light – the rest is lost as unwanted heat. Also, much of the radiation produced is invisible, limiting the bulb’s luminous efficacy to 17 lumen/Watt.
So, what was next? Along came neon and fluorescent lights – using atomic transitions in gas tubes, triggered by electric discharge – leading to more durable and more energy-efficient light sources, with the ability to create bright white light. The downside? These light sources are fragile, and can contain hazardous elements. Their light also appears less natural due to spikes in their emission spectra.
Most recently, LED light sources have taken the forefront. Light Emitting Diodes are semiconductor light sources. In the 1960s, LEDs could only emit infrared, and then red, light – they were mainly used as indicators for electronic devices. It took more than 30 years to develop an LED light source that could be used for general purpose lighting – read the article to find out exactly how this was done.
The incandescent light bulb is expected to become history, thanks to LEDs, with their high luminous efficacy of 300 lumen/Watt and far longer lifetimes.
Are they perfect? Unfortunately not. There are concerns that the UV component of white light LEDs may be damaging to eyes and skin. And while the LED’s emission spectrum is smoother than that of neon or fluorescent lighting, and so its light looks more natural, it isn’t as smooth as the light generated by an incandescent light bulb. Constant research and development aims to improve LEDs even more, and we’re excited to see that happen.
Interested in hearing more? Read the full article.
We just need your phone...After entering the number, the mobile send button will be available to you in all items.
Send to mobileAfter a short one-time registration, all the articles will be opened to you and we will be able to send you the content directly to the mobile (SMS) with a click.We sent you!The option to cancel sending by email and mobile Will be available in the sent email.00:0003:03
60% CompleteSoon... -
Ophir Blog
Affordable, sustainable laser welding and cutting
Manufacturers are turning to just-in-time production to meet the needs of complex, ever-changing supply chains. This means the production process has to be extremely efficient &...
02:54Affordable, sustainable laser welding and cuttinghttp://summur.ai/lFYVYAffordable, sustainable laser welding and cuttingManufacturers are turning to just-in-time production to meet the needs of complex, ever-changing supply chains. This means the production process has to be extremely efficient – and smooth – with every component coming out just right.
For processes using laser cutting and welding, this involves using laser measurements to make sure the laser is interacting correctly with the materials being processed. For an efficient system, automated measurements are ideal – but these are often costly.
Let’s take a look at Ophir’s article, which highlights how laser cutting and welding processes can be kept running at maximum performance, while still being both affordable, and sustainable.
Quality problems are often the heart of component failure – slowing down production lines. Sadly, in many cases, quality control lags behind the advanced laser technologies. If systems are rarely tested, and outdated measurement systems are used – there’s a real risk of creating subpar products which would slow down the production lines and cause many unhappy customers.
Especially when it comes to the high power lasers used in industrial processes, tight tolerances must be met – and that can only be done if continuous beam profiling is performed.
If thermal changes occur, early awareness and preventative maintenance is key to making sure the finished components are not affected.
So, how can this be done without going over budget?
Ophir brings hope with its BeamWatch contactless measurement system, based on Rayleigh scattering – the scattering of electromagnetic waves by particles smaller than the radiation’s wavelength, such as oxygen or nitrogen molecules in the air. It can take real-time laser profiling measurements without touching the laser beam.The BeamWatch Integrated takes this once step further, as it can be integrated into automated production lines, for super efficient and high quality processes.
Not only are these systems affordable in themselves - but laser monitoring also saves money down the line – as any quality problems can be detected as early as possible, leading towards zero-defect production – perfect for efficient, just-in-time production lines.
And – as contactless measurement systems don’t touch the laser beams, they don’t degrade over time - - making them sustainable too, with no need for maintenance.
See the article to find out more about this incredible technology.
We just need your phone...After entering the number, the mobile send button will be available to you in all items.
Send to mobileAfter a short one-time registration, all the articles will be opened to you and we will be able to send you the content directly to the mobile (SMS) with a click.We sent you!The option to cancel sending by email and mobile Will be available in the sent email.00:0002:54
60% CompleteSoon... -
Ophir Blog
Top tips for a damage-free thermal sensor
Did you know that a thermal sensor can be used for many years, without the need for a single repair? Let’s take a look at Ophir’s article on avoiding thermal sensor ...
02:39Top tips for a damage-free thermal sensorDid you know that a thermal sensor can be used for many years, without the need for a single repair?
Let’s take a look at Ophir’s article on avoiding thermal sensor damage - and find out what expert technicians have to say about keeping your thermal sensors in top condition for years to come.
According to the experts, thermal sensor damage comes from incorrect laser optical setup and usage. The articles discusses the most common causes of incorrect usage, and preventative measures you can use to keep your thermal sensors in pristine condition.
First up – surface contamination. It’s very common for thermal sensors to get dirty. It’s important to find our the source of this contamination – and take measures to prevent it. For example, in the metalworking industry – welding too close to a sensor can easily contaminate it, and should be avoided.
Preventing sensor contamination is easy – clean the sensor regularly, use a protective housing, store it in a clean, closed container when not in use - and avoid touching it with your bare hands.
Another common cause of issues is overheating the sensor.
If you use your thermal sensor at power levels that are too high, for a long period of time, you’re likely to see damage to the absorber layer.
And – if your sensor is one that uses thermal grease for thermal coupling – you’ll start to see grease contamination too.
Always keep to the power range and power density threshold listed in the sensor’s specifications.Some high power sensors require water cooling. You should make sure the water you use meets quality requirements - otherwise it can cause significant damage.
Only deionized and filtered water should be used - the water should be clean, clear, and sediment free and for deionized water it’s also important to maintain a neutral pH level.
When it comes to a damaged sensor – it’s always worth getting it tested – some sensor damage is only cosmetic, and doesn’t affect the reliability of measurement results. Other forms of damage require full sensor disc replacement.
Take a look at the full article to see pictures of different types of sensor damage, and read more details about the measures you can take to keep your sensors in pristine condition.
We just need your phone...After entering the number, the mobile send button will be available to you in all items.
Send to mobileAfter a short one-time registration, all the articles will be opened to you and we will be able to send you the content directly to the mobile (SMS) with a click.We sent you!The option to cancel sending by email and mobile Will be available in the sent email.00:0002:39
60% CompleteSoon... -
Ophir Blog
Fighting viruses with UV-LEDs
Fighting viruses has been on everyone’s mind since the COVID-19 pandemic began. Let’s explore Ophir’s article on how UV light can be used for this noble cause. ...
02:23Fighting viruses with UV-LEDsFighting viruses has been on everyone’s mind since the COVID-19 pandemic began. Let’s explore Ophir’s article on how UV light can be used for this noble cause.
As early as the 19th century, we’ve known that viruses are sensitive to heat and UV light. But how can that knowledge be translated into something actionable in the fight against viruses like COVID-19?
Well, primarily, it’s good for disinfecting things. Usually, a place like a hospital would rely on harsh chemical disinfectants – but UV light is pretty good at it too.
There have been studies on different coronaviruses over the years that have proved that these viruses are indeed sensitive to UV-C light. As long as a high enough irradiation and irradiation period are used, coronaviruses can be curbed considerably.
UV light is indeed already used for hygiene purposes – to disinfect water and surfaces. Read the full article to find out more about the parameters needed to get this job done.
So, how do we get these UV rays in the first place? For a long time, mercury vapor lamps have been used to produce UV-C light and kill microorganisms, such as viruses. In future, UV-C LEDs might become more popular, as they have a long service life, can be dimmed, and their peak wavelengths can be adjusted.
Of course, the UV rays must be measured – to ensure safe and effective disinfection – what kind of measurements are needed? Intensity, dose, and the radiant power of divergent light sources, to name a few. Ophir’s various power and energy measuring devices and integrating spheres are well suited to this important task – click on the link in the article to see more details.
Only time – and lots of research - can tell us if UV-LEDs will help fight pandemics such as COVID-19. With Ophir’s measurement equipment, maybe we’ll get there that bit sooner!
We just need your phone...After entering the number, the mobile send button will be available to you in all items.
Send to mobileAfter a short one-time registration, all the articles will be opened to you and we will be able to send you the content directly to the mobile (SMS) with a click.We sent you!The option to cancel sending by email and mobile Will be available in the sent email.00:0002:23
60% CompleteSoon... -
Ophir Blog
When laser measurements are a must for materials processing
“If you can’t measure it, you can’t improve it”. Those are the words first spoken by William Thomson, a 19th century British physicist, also known as Lord ...
02:57When laser measurements are a must for materials processinghttp://summur.ai/lFYVYWhen laser measurements are a must for materials processing“If you can’t measure it, you can’t improve it”. Those are the words first spoken by William Thomson, a 19th century British physicist, also known as Lord Kelvin.
When it comes to improving laser-based processes, in the field of materials processing – these words certainly ring true.
Let’s explore Ophir’s article and find out how, and when, these measurements must absolutely, positively be made.
The way the laser light is applied to the material being processed is measured as a function of power density, or energy density. If the laser power or beam size change over time, the new power density will affect the way the laser light is applied to the material – causing unexpected results. This makes it extremely important to collect and apply laser measurement data at certain times in a laser’s lifecycle, to ensure the process is consistent.
The article lists five stages when laser measurement is essential.
One - during application development – as the precise implementation of key performance parameters will determine the productivity of the laser system.
Two - when the laser source is integrated in the system – at this point, the parameters of the developed application are usually transferred to a very similar laser for use in the actual system, so measurements should be retaken and compared, to ensure they remain the same.
Three - during system runoff, delivery and movement – before the system is accepted by the customer, to ensure it meets the required criteria.
Four – periodically during productive use, as components may degrade over time, and debris can collect, affecting performance.
And finally, five – for preventative and corrective maintenance – a comprehensive maintenance routine protects the laser. Measurements before and after the maintenance can validate the system’s performance.
Read the article to find out more about each of these stages.
Another important factor is the repeatability of the measurements – they must be reliable, and easy to perform, to ensure consistent results. One tool suited to this task is Ophir’s BeamWatch laser beam profiler – as it provides real-time, non-contact measurements, and is very simple to set up. Follow the link in the article for more information.
There’s no question that materials processing demands reliable and frequent laser measurements – throughout the laser’s lifetime – and luckily, Ophir offers tools to suit every system.
We just need your phone...After entering the number, the mobile send button will be available to you in all items.
Send to mobileAfter a short one-time registration, all the articles will be opened to you and we will be able to send you the content directly to the mobile (SMS) with a click.We sent you!The option to cancel sending by email and mobile Will be available in the sent email.00:0002:57
60% CompleteSoon... -
Ophir Blog
How Consistent Measuring Ensures the Quality of Medical Lasers
Over the past several years, the fields of aesthetic medicine, surgery and cosmetics have been revolutionized by laser technology. With the development of their innovative laser ...
08:43How Consistent Measuring Ensures the Quality of Medical Lasershttp://summur.ai/lFYVYHow Consistent Measuring Ensures the Quality of Medical LasersOver the past several years, the fields of aesthetic medicine, surgery and cosmetics have been revolutionized by laser technology. With the development of their innovative laser systems, Asclepion Laser Technologies contributes greatly to patient well-being and faster healing. A consistent measurement strategy, effective testing processes and first-class measuring devices guarantee the high quality of the company's manufacturing at all times. For decades, Asclepion has relied on Ophir measuring technology from MKS Instruments to check the power and energy of the laser beam. To adjust it's PicoStar® laser, the company measures and analyzes the beam profile of this pico-second laser using an Ophir CCD camera combined with a beam reducer.
Asclepion Laser Technologies has been active in the area of international medical laser technology since 1977. The company's home base in the Jena Optical Valley promises – and delivers – extraordinary strength in innovation: The laser systems and their components are developed and manufactured almost entirely in-house. Over the past few years, the breadth of the company's portfolio has grown steadily; today it ranges from CO2 and solid-state lasers for dermatological and surgical procedures to diode lasers, for example for vascular applications and permanent hair removal. And it has expanded its offerings for the field of dermatology with the development of a picosecond laser: The PicoStar laser effectively and gently removes tattoos, permanent makeup and benign pigmentation.
A necessary condition for the great success of Asclepion Laser Technologies is the continued maintenance of strict quality standards. To this end, the company has developed a finely tuned measuring and testing process to which every laser system is subjected before being shipped. It rests on three essential pillars:
• Consistent measuring technology from development through to maintenance
• The right measuring technology for each application
• Meticulous quality inspection, based on the principle of double checksDuring production and, above all, during the final inspection of the laser systems, the measured parameters are continually compared against the specifications. To prevent influences due to measurement tolerances, calibrated systems of the same type are used to measure both prototypes still in development and finished laser systems before shipping or during commissioning or maintenance at the user's site.
When selecting a supplier, Roman Roth – process engineer at Asclepion and the person responsible for the proper and smooth running of manufacturing processes – has several prerequisites: "On the one hand, all our departments need reliable measurement equipment to provide us with accurate and repeatable results. At the same time, our wide range of laser types means that we need many different measurement methods. With MKS, we know that our demands – in terms of both the quality and the diversity of measurement solutions – can be met with standard Ophir sensors or individualized approaches" For example, to measure the power of an Asclepion diode laser, the company uses an MKS thermal sensor, such as the Ophir L50(300)A. The same measuring principle is also applied to solid-state lasers for surgery.
The pulsed solid-state lasers used in dermatology, on the other hand, are measured with pyroelectric sensors. Because of the high power and energy densities involved, Asclepion relies on Ophir sensors of the type PE50BF-DIFH-C, PE50- DIF-ER-C, which have integrated diffusers and thus higher damage thresholds. In order to meet the special requirements of medical technology, the sensors are also adjusted for specific wavelengths, e.g. calibrated to 2940 nm.
Asclepion's collection of metrological solutions for laser power and energy is rounded out with Ophir photodiode sensors. They measure the pilot beam systems that aim at the target in all solid-state lasers, the power of which is in the range of just a few mW. Depending on the area of application, Asclepion transmits the measurement data either via PC interfaces or directly to compact, handheld display devices.
No matter what measurement principle is applied, one thing is certain: Every single laser system that leaves Asclepion's production facility undergoes meticulous final testing. A final inspection protocol – encompassing some 25 to 60 A4 pages – is worked through step by step; depending on the laser system, this last evaluation can take a few days to a week. According to the principle of double checks, every product produced by Asclepion must be formally tested and finally approved by the Quality Assurance Department on the factory site before being shipped out to customers.
Introduced in 2019, the company's picosecond laser proved to be a particular challenge: In addition to the power and/ or energy of the laser beam, the beam profile must also be carefully checked and pre-adjusted on the optical bench during the final test. Here, Asclepion relies on the beam profile measurement taken by an Ophir CCD camera in combination with a beam reducer and the BeamGage or BeamMic analysis software. If, at the end of the beam path, the laser is ever to provide the optimal conditions as prescribed by the laser specifications, it must be carefully pre-adjusted in stages. For this purpose, the beam profile is recorded with the CCD camera at three different positions along the optical bench. These figures show the measurements of a correctly adjusted laser compared to that of a misaligned laser.
Without this camera-based measuring solution, it would be difficult and time-consuming to adjust the resonator on the optical bench. Too much divergence in the beam would lead to unwanted radiation of downstream optical components. Using the CCD camera saves considerable time and effort in this sensitive process while ensuring repeatable measurements of the beam profile. Also in his role as Asclepion's test equipment officer, Roman Roth is very satisfied with the collaboration: "The Ophir measuring devices work reliably and deliver reproducible results – both of which are essential in medical technology. In terms of sustainability, the quality and durability of the measurement technology are beyond reproach; we're still using our Ophir Nova display devices from 1996."
In general, the Ophir measuring instruments are in constant use at Asclepion Laser Technologies. Whether in the development phase of the laser systems, in the final test or during installation and maintenance at the customer: Any deviation from the specification is detected, and potential sources of error are eliminated immediately. In this manner, decoupling mirrors of poor quality or inhomogeneous laser crystals, for example, have been caught and rejected during final testing. Roman Roth is sure of one thing: "No matter which of our lasers it is, it's tested with at least one Ophir instrument." This makes it all the more important to regularly check the more than 100 sensors from Ophir that are currently employed throughout the various areas of Asclepion Laser Technologies. Every year, these instruments are calibrated according to specs in Ophir's European calibration laboratory in Darmstadt. This in turn guarantees the precise measurement of all Asclepion laser systems and thus their enduring quality, for the safety of operators and patients alike.
We just need your phone...After entering the number, the mobile send button will be available to you in all items.
Send to mobileAfter a short one-time registration, all the articles will be opened to you and we will be able to send you the content directly to the mobile (SMS) with a click.We sent you!The option to cancel sending by email and mobile Will be available in the sent email.00:0008:43
60% CompleteSoon... -
Ophir Blog
DiaMonTech Develops Non-invasive Blood Glucose Monitor Using M-IR Lasers
More than 400 million people worldwide suffer from diabetes. For them, the ability to measure blood glucose levels non-invasively (without piercing the skin) would be an enormous ...
08:24DiaMonTech Develops Non-invasive Blood Glucose Monitor Using M-IR Lasershttp://summur.ai/lFYVYDiaMonTech Develops Non-invasive Blood Glucose Monitor Using M-IR LasersMore than 400 million people worldwide suffer from diabetes. For them, the ability to measure blood glucose levels non-invasively (without piercing the skin) would be an enormous relief. Thanks to a patented development by DiaMonTech AG, this dream could soon come true for many people. The technology, which uses an infrared quantum cascade laser, is already available as a desktop device. But a smartphonesized instrument is soon to follow. In order to achieve this miniaturization without loss of quality, it is necessary to detect even minute changes in the laser beam. DiaMonTech used the Ophir Pyrocam to measure and characterize all their laser developments.
Many non-invasive methods for measuring blood glucose have failed because they were not accurate enough: Glucose values in body fluids such as tears, saliva or sweat do not correlate sufficiently with glucose values in blood. The situation is different for skin fluid (interstitial fluid – ISF). Measurements taken on ISF at points with good blood supply correspond well to the actual amount of glucose in the blood. DiaMonTech was founded in 2015, after years of research at the Goethe University Frankfurt. On the basis of this research, the company has developed the first noninvasive blood glucose meter, obtaining CE approval as a medical device in 2019.
The D-Base – as the desktop device is called – works based on infrared spectroscopy, and specifically the principle of photothermic deflection. For this purpose, a quantum cascade laser radiates infrared pulses in wavelengths ranging between 8 and 11μm into the deeper skin layers. The pulses of these wavelengths pass through the sensor element and excite the glucose molecules to oscillate briefly, with the fast relaxation a small amount of heat is given off to the environment. At the skin surface this results in a minimal increase in temperature. In the sensor element, the thermal gradient causes a thermal lens effect. The test beam of a red laser diode is deflected by this thermal lens as it passes through the IRE. The deflection is measured by a position-sensitive photodiode; the device calculates the glucose concentration based on the deflection.
The measuring principle has now been proven in everyday clinical practice, and numerous tests show that the measurements provide reliable results. However, as Sergius Janik, COO at DiaMonTech, explains, shrinking the size of the measuring device is still a challenge: "Diabetes patients want fast and compact measurement technology that they can easily use at home and on the road. This is the focus of all our current research." Only a few manufacturers offer the tunable quantum cascade lasers that DiaMonTech uses for the D-Base. In order to reduce the overall size of the measuring device, the laser must be as small as possible. However, the specific parameters of the laser beam must not be affected by this reduction in size. Even the classic quantum cascade lasers used thus far must meet these specifications exactly.
In order to evaluate the quality of a given quantum cascade laser, the DiaMonTech laboratory conducts detailed measurements on all of them to answer the following questions:
• What does the laser beam profile look like?
• What is the output power of the laser?
• How divergent is the beam?
• What is the pulse repetition rate?
• What is the pulse-to-pulse stability and shape of the pulse?
• How large is the focal spot on the skin?In the company's early days, the team relied on the knifeedge technique for laser measurement to obtain the beam profiles. But because the number of measuring points required is large, it takes several hours to measure a laser beam this way. Had the company applied this method in the development of its new, compact blood glucose meter, it would have lost a lot of time – and still, the results would not have been precise enough. After in-depth research and conducting an array of tests in their own laboratories, the experts decided on the Ophir Pyrocam-III-HR-C-A-PRO. Using this high-resolution pyroelectric matrix camera, the beam profile of an infrared laser can be measured both quickly and reliably. For the application at DiaMonTech, the camera was individually calibrated to the appropriate signal level. The camera data is then evaluated with the BeamGage software. Output power, beam profile and beam divergence can be determined by the camera in just a few seconds. Sergius Janik explains: "The Ophir Pyrocam is our key measuring device for characterizing the laser beam, and we use it every day. We use it not only for developing new prototypes, but also for quality assessment and troubleshooting. As necessary, we also make the Pyrocam available to our development partners, so they can make precise and reliable adjustments."
Janik describes a concrete application as an example of the enormous time savings achieved by the Pyrocam. During a series of tests conducted by the DiaMonTech lab on a new laser, the engineers were unable to focus the beam. The power distribution of the beam was very irregular, but the cause was not obvious at first glance.
Only the images taken with the Pyrocam provided an explanation. Instead of the desired symmetrical Gaussian beam profile, the beam appeared strongly distorted.
These results showed that the collimating lens of the beam was out of adjustment, which may have occurred during shipment. The laser system was sent back to the manufacturer, the lens was re-adjusted, and then the Pyrocam measurements showed a uniform beam profile.
Another challenge that arises when developing a compact blood glucose meter is the different beam position for any given wavelength. To detect glucose in the skin, it is necessary to take measurements using a variety of wavelengths in the infrared range. But with a tunable laser, as soon as the wavelength is changed, the beam moves (a.k.a. "beam hopping"). As a result, it enters the skin at a slightly different position (up to about ¼ mm) and – analogous to wrongly corrected vision – the thermal lens becomes blurred. When the DiaMonTech team changes the wavelengths, they use the Pyrocam to measure the focus position, which is marked with crosshairs. The BeamGage software records the changes in crosshair position for accurate tracking. The wavelengths that provide the most precise measurements can then be determined, based on the findings from these readings.
Faster measurements mean more efficient development:
Along the road to miniaturization in non-invasive blood glucose monitoring, there is no way around a camerabased measurement of the beam profile. Before purchasing a measuring device, DiaMonTech tested the solutions available on the market. The Ophir measuring device not only had a wavelength range suited to the purpose, it also provided the required performance range and offered very good value for the money. Janik appreciates the measurement technology: "The Pyrocam makes our daily work easier. We no longer waste hours on time-consuming measurements; rather, we get reliable results very quickly. This allows us to concentrate on the essential work of development."We just need your phone...After entering the number, the mobile send button will be available to you in all items.
Send to mobileAfter a short one-time registration, all the articles will be opened to you and we will be able to send you the content directly to the mobile (SMS) with a click.We sent you!The option to cancel sending by email and mobile Will be available in the sent email.00:0008:24
60% CompleteSoon... -
Ophir Blog
Get your laser measurement ‘content fix’ on the go with Playter!
For over a decade, our team of experts in Ophir photonics has been creating super valuable professional content (articles, white papers, blog posts, webinars) which was brought to ...
02:55Get your laser measurement ‘content fix’ on the go with Playter!http://summur.ai/lFYVYGet your laser measurement ‘content fix’ on the go with Playter!For over a decade, our team of experts in Ophir photonics has been creating super valuable professional content (articles, white papers, blog posts, webinars) which was brought to you on a weekly basis on our blog and social media channels.
Our goal is simple. Bring you the best updates, technical tips and industry news that are relevant to your daily work. Why? again, simple – We care about your success.
We want you to perform your best not only through using our top products, but also through our experts’ knowledge and tips. This is why we work tirelessly to provide you with fresh professional content each week.
It’s clear – Our readers and followers are our biggest asset.
Over the last few years something has changed.Content overloading and lack of time makes it harder for us to read thoroughly and find time to consume the information we are interested in.While text has been around us for quite a while, audio showed up recently – offering the opportunity to stay up-to-date and learn while on the go.
As you know, one of Ophir’s most important values is to stay ahead and bring you the latest technologies and innovative solutions out there, not only in laser measurement but also in content consumption.
Therefore, we decided to make it easier for you to consume our content and take a step forward into audio.
As written in the Summurai blog, “Audio opens the door to a new type of communication — one that is adapted to all types of devices, and which can fit into even the smallest parts of everyone’s timeline.”
It’s time to Meet Playter®. Thanks to our new collaboration with Summurai we can now offer you the best of Ophir’s content summarized & read to you out loud.
The Playter allows you to choose whether you’d like to read our content or listen to it, now or later, to make it easy for you to get your knowledge whenever and wherever works for you.
From now on, you’ll be able to enjoy Ophir’s most popular blog posts, white papers and articles in a more convenient way, while driving, shopping or walking your dog.
Soon, you’ll be able to create your own playlist and even share it with colleagues through social media. How awesome is that?!
You’ll be able to find our audio content on the right side bar on our blog!If you like it or want to share any comments, we’ll be more than happy to hear.
Let us know what you think and which content you’d like us to Playter for you!We just need your phone...After entering the number, the mobile send button will be available to you in all items.
Send to mobileAfter a short one-time registration, all the articles will be opened to you and we will be able to send you the content directly to the mobile (SMS) with a click.We sent you!The option to cancel sending by email and mobile Will be available in the sent email.00:0002:55
60% CompleteSoon... -
Ophir Blog
Things to remember before setting up your laser measurement equipment for the first time
It can be overwhelming to figure out how to set up your laser measurement system for the first time. Let’s take a look at an article in which John McCauley, a Bus Dev ...
02:46Things to remember before setting up your laser measurement equipment for the first timehttp://summur.ai/lFYVYThings to remember before setting up your laser measurement equipment for the first timeIt can be overwhelming to figure out how to set up your laser measurement system for the first time.
Let’s take a look at an article in which John McCauley, a Bus Dev manager at Ophir, revisits a product demonstration in which he had to confidently set up equipment to show a prospective customer. He used this experience to come up with a list of things to remember before setting up your equipment for the first time.
Before you even choose your equipment, it’s crucial to understand how your laser works.
Every laser has difference characteristics – is it continuous wave, or pulsed, for example. What is its power, energy, wavelengths?
How are you going to use the laser? What’s the application, and what does that mean for the laser?
If you’re using it for materials processing, you’re like to have a laser light coming out of a processing head, converging on a focused spot – the amount of light and the size of the focus spot are important things to know.
Once you understand your laser, it’s time to understand the whole laser system. Many times a measurement system is chosen after a laser system has already been designed and commissioned, so it has to fit in with the system and its limitations.
There are some characteristics that can create new challenges – glovebox welding lasers, for example, have a processing head at an offset, and a beam profiling system would need to be set up with this in mind.
The last thing you must remember is to know your measurement product limitations. Whatever happens - you mustn’t exceed your measurement product’s rated damage threshold by applying to high a power density. Measurements don’t need to be taken at the focus, where power density is highest – as laser power or energy will be the same whatever the beam size. The smaller the beam size, the higher the power density, the more chance of exceeding the measurement equipment damage threshold – which is not good for the equipment, or the measurements you’re taking.
Well armed with knowledge about your laser, laser system, and the laser measurement tools being used – setting up your laser system will be far less daunting.
Read the article for more details about this important information.
We just need your phone...After entering the number, the mobile send button will be available to you in all items.
Send to mobileAfter a short one-time registration, all the articles will be opened to you and we will be able to send you the content directly to the mobile (SMS) with a click.We sent you!The option to cancel sending by email and mobile Will be available in the sent email.00:0002:46
60% CompleteSoon... -
Ophir Blog
A beginner’s guide to laser power measurement
If you’re a serious laser user, you’ll know how important it is to measure certain laser parameters. Of those parameters, laser power is the most simple way to ...
02:45A beginner’s guide to laser power measurementIf you’re a serious laser user, you’ll know how important it is to measure certain laser parameters. Of those parameters, laser power is the most simple way to understand your laser. With the help of Ophir’s blog post – the beginner’s guide to laser power measurement, let’s talk about the first step in setting up a laser power measurement system – choosing the tools you’re going to use – the meter, or interface, and the sensor.
The meter, or interface, measures electric current, and displays the result. Ophir has a whole range of meters and PC interfaces, to suit any setup. There’s a link to the full list in the blog post.
Then – there’s the more complex choice – the sensor itself. The sensor must measure laser power accurately, and convert it to electric current – as that’s what the meter, or interface, reads.
If you’re looking for an easy way to make this choice – you’re in luck. There’s a link in the blog post to Ophir’s sensor finder, which allows you to enter your laser’s parameters and find the ideal sensor for your system.
What’s going on behind-the-scenes to generate these ‘best matches’?
Well, to start off with, there are two types of sensors to choose from – photodiodes, or thermopiles. What’s the difference?
If you have a low power laser, you’ll need a photodiode-based sensor, known as a PD sensor – for one simple reason – it’s the only type sensitive enough to measure lower power lasers.And conversely, a thermopile-based sensor, or thermal sensor, is less sensitive, but can measure far higher powers – making it the choice for high power lasers.
When it comes to lasers with continuous wave beams, there are three crucial parameters that need to be considered, for either type of sensor.
First, the sensor must be able to cover the wavelength used by your laser. Secondly, the sensor must work well for your laser’s power range. And finally, it must be the right diameter, so that it can fit into the laser aperture.
For pulsed beams, things get a bit more complicated, but that’s a story for another day.
We just need your phone...After entering the number, the mobile send button will be available to you in all items.
Send to mobileAfter a short one-time registration, all the articles will be opened to you and we will be able to send you the content directly to the mobile (SMS) with a click.We sent you!The option to cancel sending by email and mobile Will be available in the sent email.00:0002:45
60% CompleteSoon... -
Ophir Blog
A complete toolkit for measuring and testing VCSELs
A VCSEL – a Vertical Cavity Surface Emitting Laser – is a semiconductor laser diode that can be packaged as hundreds of emitters on a single chip. This makes it useful ...
02:58A complete toolkit for measuring and testing VCSELshttp://summur.ai/lFYVYA complete toolkit for measuring and testing VCSELsA VCSEL – a Vertical Cavity Surface Emitting Laser – is a semiconductor laser diode that can be packaged as hundreds of emitters on a single chip. This makes it useful for a whole range of applications – including face recognition, proximity sensors, and augmented reality displays – all features you may well find on your smartphone. To maximize device battery life, it’s crucial to measure VCSEL power consumption, and keep it low.
However, testing and a measuring a VCSEL has its challenges – the beams can be very wide, and are often used in pulsed mode.
Let’s dive into Ophir’s article, which explains the tools you need to measure VCSELs, despite these challenges.First up – power consumption.
An integrating sphere is used for collecting light at high angles, often with a suitable port adapter to support the VCSEL’s wide beam angles. The sphere is coupled with a photodiode detector, which can measure even the lowest power lasers – down to under 1 microwatt!You can also add other tools, such as spectrometers, to the sphere - and take multiple measurements at once.
For power levels above 100 milliwatts, you could choose a thermophile sensor instead - these are more compact and easy to use than integrating spheres.
Next - If the VCSEL is operating in pulsed mode - you may need to measure the energy per laser pulse – this can be done using pyroelectric and photodiode energy sensors.
For analyzing laser beam size, quality, shape, and divergence - beam profiling is essential. This is best done using a suitable camera, with Ophir’s BeamGage software for analysis. Why a camera? It’s the ideal way to get real-time, accurate measurements of the laser beam profile. See the article to find out about different methods for VCSEL beam profiling.
When it comes to measuring pulse shape and noise, you’ll need a high speed photodiode detector, which can be attached to an integrating sphere, or used in free space. Pair it with analysis in either the time or frequency domain.
Often, laser system manufacturers build measurement capabilities into their laser systems – Ophir offers these OEM solutions - to provide robust laser performance analysis and fast feedback for system control.
Visit the full article to read about Ophir’s VCSEL measurement solutions in further detail.
We just need your phone...After entering the number, the mobile send button will be available to you in all items.
Send to mobileAfter a short one-time registration, all the articles will be opened to you and we will be able to send you the content directly to the mobile (SMS) with a click.We sent you!The option to cancel sending by email and mobile Will be available in the sent email.00:0002:58
60% CompleteSoon... -
Ophir Blog
Let’s get started with laser beam profiling
We’d all like it if lasers always worked as they were supposed to – but that’s not always the case. So, like any process, we need some kind of process control &...
02:57Let’s get started with laser beam profilingWe’d all like it if lasers always worked as they were supposed to – but that’s not always the case. So, like any process, we need some kind of process control – with lasers, you’ll want to be taking accurate measurements.
You might think measuring laser power is enough – but that leaves a lot of the story untold. Instead, laser beam profiling gives you more insight. Let’s explore Ophir’s blog post, and discover how to get started with laser beam profiling.
Let’s imagine a laser as a perfect, idealized beam of light – if something goes wrong, you’ll tweak the power and it will be fixed – right? Unfortunately, it’s not so simple. Lasers degrade with time, and that can change the beam’s spot and shape.
Increasing the beam’s power could even make the shape worse.
Beam profiling is the secret to monitoring laser beam size and shape, to ensure that the beam continues to look and behave exactly as designed.
So, how do you get started in implementing a profiling solution? First, you need to choose the right equipment – and to do that, you need to decide the measurements you’re planning to take. This could include beam width, overall beam shape, ellipticity, and M-squared – the beam quality factor. Most beam parameters are based on these measurements.
Then, it’s time to choose a beam profiler. Most profilers measure beam width – but in different ways. There’s a link in the blog post that explains this further.
Scanning slit profilers take tiny samples of the beam through two narrow slits, creating two one-dimensional profiles on the X-axis and Y-axis. You can use these to create a two dimensional image, but that doesn’t provide a full picture.
CCD cameras can product a full two dimensional image of the laser. But, they require that high power lasers have more attenuation, which can be a hassle. And very small lasers, such as those that are tens of microns, might do better with scanning slits - for higher resolution.
Both scanning slits and CCD cameras can be used to measure ellipticity and M-squared, although M-Squared requires the addition of an optical rail or mirror system to make measurements at multiple locations.
If you’re not sure where to start - visit the blog post and click on the link at the bottom to talk to an Ophir expert.
We just need your phone...After entering the number, the mobile send button will be available to you in all items.
Send to mobileAfter a short one-time registration, all the articles will be opened to you and we will be able to send you the content directly to the mobile (SMS) with a click.We sent you!The option to cancel sending by email and mobile Will be available in the sent email.00:0002:57
60% CompleteSoon... -
Ophir Blog
The alarming shortage of semiconductor chips
As part of a series of blog posts on future trends, Ophir, an MKS company, has raised awareness of an alarming concern – the worldwide shortage of semiconductor chips. These ...
03:01The alarming shortage of semiconductor chipsAs part of a series of blog posts on future trends, Ophir, an MKS company, has raised awareness of an alarming concern – the worldwide shortage of semiconductor chips. These chips are used everywhere – from phones, laptops, and PCs – through to vehicles, washing machines, ATMs, and more.
Let’s find out how this shortage came about, what effects it is having on our world, and see how key players are stepping in to resolve it.
Like many of today’s issues, the trigger behind the semiconductor shortage was the COVID-19 pandemic.
During the pandemic, demand for laptops and computers surged. But this shortage didn’t just affect the production of personal computers, it also had a knock-on effect on other industries.
For example, a new car build typically contains up to 1500 different semiconductor chips. Delivery lead times for chips have gone from an average of 9 weeks, to a staggering 22 weeks.
The result? Delays in the production of over 1 million vehicles in North America alone, with worldwide manufacturers projected to lose about 210 billion dollars in sales.
In China, chip supply chain disruptions caused electricity shortages, leading the government to introduce rationing, ordering factories to work less hours per day. And yes, this has caused Chinese chip manufacturers to reduce their production, creating a catch-22 situation, where the chip shortage is getting harder to resolve.
With these issues creating havoc worldwide, key players have stepped in to assist. Among them - Intel has invested 20 billion dollars in two huge new semiconductor fabrication plants in Arizona.
Samsung Electronics has planned to triple their production capacity by 2026. And TSMC, the largest contract chipmaker in the world, have joined forces with Sony to invest 7 billion dollars in creating a factory in Japan.
Other companies are also ramping up production – SK Hynix, Micron Technology, Bosch, and Hyundai. You can read more about their efforts in the original blog post.
As key suppliers of semiconductor components, MKS also has an important role to play – and is well positioned to support these ongoing industry-wide efforts to increase production.
It’s our hope that with a joint effort, these companies will be able to mitigate the supply chain disruptions that we see today, and get semiconductor production back on track.
We just need your phone...After entering the number, the mobile send button will be available to you in all items.
Send to mobileAfter a short one-time registration, all the articles will be opened to you and we will be able to send you the content directly to the mobile (SMS) with a click.We sent you!The option to cancel sending by email and mobile Will be available in the sent email.00:0003:01
60% CompleteSoon... -
Ophir Blog
The secret to speedy laser process development
Anyone involved in automotive manufacturing knows how crucial it is to be able to weld efficiently and accurately. Especially when laser seam welding sheets of zinc-coated steel, a...
02:51The secret to speedy laser process developmentAnyone involved in automotive manufacturing knows how crucial it is to be able to weld efficiently and accurately. Especially when laser seam welding sheets of zinc-coated steel, a common occurrence in the industry, there are many challenges – as these metals have disparate melting and evaporation properties.
Let’s explore this case study, which shows how Volkswagen’s team of experts in Wolfsburg took on an exciting research project – to develop a new and unique multi-focal laser welding process.
Project leader and engineer Alexander Franz immediately recognized the importance of measurement technologies in laser process development. The time taken to measure a laser has a direct effect on the overall process development time. To speed up development – the team chose Ophir’s BeamWatch laser measurement instrument.
The idea behind multi-focal laser welding is that several laser beams are generated at once by a laser beam optic, to join hot-dip galvanized sheets in a zero-gap configuration. Using two highly focused forward laser beams, and one welding spot, two and three sheet metal joints can be produced with extremely high seam quality.
What the secret to this impressive result? Keeping the geometry of the laser beams completely in sync – and to do that, you need to measure them. You can read the full case study to find out more about the types of measurements taken.
Ophir’s BeamWatch has unique properties which made it suited for this task – it measures the laser beams without touching them, and allows multiple beams to be measured at once.
Each measurement could be taken and displayed in less than 400 milliseconds. This is a massive improvement when compared to the five minutes or more it would take for each measurement, when using other measurement instruments.
In effect, with the BeamWatch, the team was able to see the results of every tiny change they made to the process in real time. Thanks to this – they developed and refined the new welding process very quickly.
Of course, the automotive industry is not the only application the BeamWatch is suited to – it’s compact, flexible, and easy to set up – making it ideal for troubleshooting and laser process development in any field.
We just need your phone...After entering the number, the mobile send button will be available to you in all items.
Send to mobileAfter a short one-time registration, all the articles will be opened to you and we will be able to send you the content directly to the mobile (SMS) with a click.We sent you!The option to cancel sending by email and mobile Will be available in the sent email.00:0002:51
60% CompleteSoon... -
Ophir Blog
How we found the right beam profiling solution for a nuclear-powered US Army submarine
The right beam for a super specific and complex military challenge
02:42How we found the right beam profiling solution for a nuclear-powered US Army submarinehttp://summur.ai/lFYVYHow we found the right beam profiling solution for a nuclear-powered US Army submarineHow we found the right beam profiling solution for a nuclear-powered US Army submarine
This case study follows the journey of the Ophir team, as they worked tirelessly to find the right beam profiling solution for a nuclear-powered submarine.
You’ll find out the winning combination of technologies, tools, and techniques that were used to carry out this challenging task.
The US Army embraces emerging technologies – and so, the Ophir team ended up looking into laser measurements for a laser in the periscope of a 6800 ton, nuclear-powered submarine.Of course, as with any military application, there are strict requirements to meet. In this case, the laser had to be extremely accurate.
As you can imagine, there are few things more challenging than ensuring high laser accuracy on a moving, underwater vehicle.
This laser operates in conditions with limited inputs - GPS data, and the influence of gravity on its orientation and alignment.
As a result, the quality of the laser beam - and its shape, size, and intensity - all become critical - and beam alignment must be measured with extremely high accuracy.Finding the right instrumentation for these measurements wasn’t easy!
After several attempts, the Ophir team discovered a winning combination - Ophir-Spiricon BeamGage software, together with the Spiricon SP300 - a high-speed, high-resolution USB3 CCD camera.
Three key measurements were taken - a baseline source beam measurement, the beam’s ellipticity, and the laser source’s Gaussian Fit.
Next, these measurements were repeated at greater distances from the source, to calculate changes, and see if these changes were within tolerance. This method allowed them to capture both qualitative and quantitative differences, so the source could be improved and adjusted.
The beam profiling software proved itself vital for capturing the measurements and images needed. This data was used to identify the critical variables, from both the laser source and the final assembly, which would have an impact on the system.
With the right technologies, techniques, and tools - the team was able to ensure maximum laser system performance for this challenging underwater military application.
Take a look at the original case study – where you’ll see some of the measurements captured, in their graphical form.
Dick RieleyEast Coast Regional Sales Manager, Ophir Photonics GroupWe just need your phone...After entering the number, the mobile send button will be available to you in all items.
Send to mobileAfter a short one-time registration, all the articles will be opened to you and we will be able to send you the content directly to the mobile (SMS) with a click.We sent you!The option to cancel sending by email and mobile Will be available in the sent email.00:0002:42
60% CompleteSoon...
-
Ophir by MKSOphir Power/Energy Meter Calibration Procedure
When it comes to laser measurement systems, accuracy is super important. A world-leader like Ophir uses strict ...
02:37Ophir Power/Energy Meter Calibration ProcedureWhen it comes to laser measurement systems, accuracy is super important. A world-leader like Ophir uses strict processes to ensure measurement accuracy and analyze – and quantify - calibration errors. Let’s look at Ophir’s article and see how they’re making sure their laser power and energy meters meet specifications.
The total accuracy of measurement is influenced by many different factors – such as wavelength, sensor linearity, uniformity of readings over the surface, pulse rate, display unit calibration uncertainty, damage done to the absorber surface, and electromagnetic interference. The article describes all of these factors, and how they are handled when it comes to Ophir sensors – read the article in full to find out more.
The article primarily discusses two factors – firstly – the power calibration uncertainty of the measuring sensor at the power level, energy level, and wavelength at which it was calibrated, and secondly - the energy calibration uncertainty – this is the extra error due to the extra calibration step needed to calibrate energy.
Ophir’s accuracy specifications are in general “2 Sigma”. This means that, statistically, in 95% of cases the error of the system measured will not exceed the stated error. For example, if the stated error is plus minus 3 percent, then in 95% of cases, it will not exceed 3%, and in 99% of cases, it will not exceed 4%.
Ophir goes to great lengths to ensure sensors are calibrated to meet strict requirements. The possible errors are analyzed using advanced statistical techniques, resulting in highly accurate and reliable specifications. This is done for all types of sensors, and the article outlines the exact calculations made, as well as the resulting expected error, for each type of Ophir measurement device.
If you’re interested in knowing all of the hard work that goes into ensuring that Ophir’s high quality laser measurement devices have accurate specifications and minimal total error, be sure to check out the article.
We just need your phone...After entering the number, the mobile send button will be available to you in all items.
Send to mobileAfter a short one-time registration, all the articles will be opened to you and we will be able to send you the content directly to the mobile (SMS) with a click.We sent you!The option to cancel sending by email and mobile Will be available in the sent email.00:0002:37
60% CompleteSoon... -
Ophir by MKSSo you want to convert a laser wavelength?
The wavelength of a laser is one of its fundamental characteristics. Laser diodes, one of the most common laser ...
03:22So you want to convert a laser wavelength?The wavelength of a laser is one of its fundamental characteristics. Laser diodes, one of the most common laser sources, have wavelengths determined by their design and the materials they are made from. But what happens when you need a specific wavelength for your application, and the laser can’t generate it? That’s where laser wavelength conversion is used. Let’s take a look at Ophir’s article and find out how this is done.
First, let’s talk about tuneable lasers. Some lasers can be tuned, although the tuning range is limited by the gain medium bandwidth. The tuning is done by controlling loss in the laser cavity so it’s minimized for the wavelength at which lasing occurs. Tuning mechanisms can include controlling the laser’s temperature, or using microelectromechanical actuators to change the cavity’s length.
Most solid state lasers are not tuneable, as they have a narrow gain spectrum. One exception is the Ti-Sapphire laser which has a wide gain bandwidth and can be tuned between 650-1100 nanometers.
Linear wavelength conversion involves using the laser to pump a gain medium, such as a crystal, to a higher energy state – and the excited electrons then decay to a lower energy state by emitting radiation at a longer wavelength. Put the gain medium in a cavity, and a laser is formed. An example is the Nd-YAG laser, which is pumped by a laser diode at 808 nanometers and emits radiation at 1064 nanometers.
Next, we have nonlinear wavelength conversion, such as second-harmonic generation (SHG). A well-known example is the green laser that that uses a nonlinear crystal to convert 1064 nanometers to 532 nanometers. There are many requirements involved in this type of conversion, such as meeting phase matching conditions – read the article to find out more.
Lastly, we have non-coherent laser-driven light sources. One example is the generation of plasma that emits extreme ultraviolet radiation at a wavelength of 13 nanometers. This plasma is generated by focusing a high power CO2 laser, with a wavelength of about 10 micrometers, onto tin droplets in a vacuum – resulting in EUV light that enables advanced photolithography in the microelectronics industry. Read more about it in the article.
So, to round it up – it’s not always possible to get the wavelength you need for a specific application, due to limitations in the laser and in the materials and processes involved. But, nonlinear optical elements can allow the laser industry to reach further into more wavelength regions, enabling processes that are otherwise impossible to attain.
We just need your phone...After entering the number, the mobile send button will be available to you in all items.
Send to mobileAfter a short one-time registration, all the articles will be opened to you and we will be able to send you the content directly to the mobile (SMS) with a click.We sent you!The option to cancel sending by email and mobile Will be available in the sent email.00:0003:22
60% CompleteSoon... -
Ophir by MKSMeasurement tools? Lasers are leading the way
Lasers are used in so many ways, from optical fiber internet to performing sophisticated medical procedures. But they...
03:12Measurement tools? Lasers are leading the wayLasers are used in so many ways, from optical fiber internet to performing sophisticated medical procedures. But they’re also superstars in another field – measurements. Let’s explore Ophir’s article on lasers as measurement tools.
Laser-assisted measurements can enhance and improve the way physical quantities are measured. They can calculate the distance between objects, using different methods depending on the size of the object, it’s distance from the measurement device, and the required resolution.
For example, there’s LiDAR – which encompasses a range of techniques for generating 3D maps of the environment, based on projecting laser light and detecting the reflected signal. It’s often used for autonomous vehicle navigation, to determine the best and safest driving strategy.
Lasers have been useful in other fields of measurement – such as interferometry, spectroscopy, microscopy, and atomic clocks.
Interferometry relies on superimposing electromagnetic radiation that has traversed different optical paths, and extracting information from the resulting interference pattern. The world’s most advanced interferometer stands in the heart of the Laser Interferometer Gravitational-Wave Observatory experiment. It can detect gravitational waves due to the change they exert on a laser beam that travels in one of its four-kilometer-long interferometer arms, measuring changes in optical path of less than one ten thousandth of the size of a proton! Read the article to find out more.
Spectroscopy is the study of interaction between light and matter – a laser with a well-defined wavelength can be used to investigate energy gaps between two electronic states of atoms or molecules. This technology has allowed scientists to catalog atomic and molecular transitions of almost every element and molecule known to us.
Microscopy is the use of microscopes to magnify objects. At first, microscopes used only lenses to view the object with visible light, and their maximum resolution was limited by diffraction due to the wave nature of light. But super-resolution microscopes, using lasers, have found ways to surpass the diffraction limit, with incredible results.
Lastly – lasers play a key role in atomic clocks – the most precise time-measurement system device built by man. Atomic clocks use the known energy-level differences of certain atoms to generate a highly stable and repeatable signal, with a known frequency - from which time can be measured. Read the article to find out more about the laser’s involvement in this fascinating application.
All in all, lasers have contributed greatly to developing measurement tools that go above and beyond the capabilities of other measurement technologies.
We just need your phone...After entering the number, the mobile send button will be available to you in all items.
Send to mobileAfter a short one-time registration, all the articles will be opened to you and we will be able to send you the content directly to the mobile (SMS) with a click.We sent you!The option to cancel sending by email and mobile Will be available in the sent email.00:0003:12
60% CompleteSoon... -
Ophir by MKSA journey through the evolution of man-made light sources
Since the beginning of time, man had busied itself with creating light sources. Let’s travel through time using...
03:03A journey through the evolution of man-made light sourcesSince the beginning of time, man had busied itself with creating light sources. Let’s travel through time using Ophir’s article to explore the man-made light sources of the past, present, and future.
The earliest light sources were of course fire-based. The humble fire served as a light source, but also provided heat for cooking and warmth. Then, candles and oil lamps allowed fire to be controlled just for the purpose of providing light.
Moving on to the beginning of the 19th century, gas lanterns appeared in the streets of major European and American cities.
At the end of the 19th century, the incandescent light bulb made its first appearance – the rise of the electric light. 140 years later, we still use these bulbs. However, there are some problems – with electric current transmitting through a highly-resistant filament, only a very small portion of electrical energy is made into light – the rest is lost as unwanted heat. Also, much of the radiation produced is invisible, limiting the bulb’s luminous efficacy to 17 lumen/Watt.
So, what was next? Along came neon and fluorescent lights – using atomic transitions in gas tubes, triggered by electric discharge – leading to more durable and more energy-efficient light sources, with the ability to create bright white light. The downside? These light sources are fragile, and can contain hazardous elements. Their light also appears less natural due to spikes in their emission spectra.
Most recently, LED light sources have taken the forefront. Light Emitting Diodes are semiconductor light sources. In the 1960s, LEDs could only emit infrared, and then red, light – they were mainly used as indicators for electronic devices. It took more than 30 years to develop an LED light source that could be used for general purpose lighting – read the article to find out exactly how this was done.
The incandescent light bulb is expected to become history, thanks to LEDs, with their high luminous efficacy of 300 lumen/Watt and far longer lifetimes.
Are they perfect? Unfortunately not. There are concerns that the UV component of white light LEDs may be damaging to eyes and skin. And while the LED’s emission spectrum is smoother than that of neon or fluorescent lighting, and so its light looks more natural, it isn’t as smooth as the light generated by an incandescent light bulb. Constant research and development aims to improve LEDs even more, and we’re excited to see that happen.
Interested in hearing more? Read the full article.
We just need your phone...After entering the number, the mobile send button will be available to you in all items.
Send to mobileAfter a short one-time registration, all the articles will be opened to you and we will be able to send you the content directly to the mobile (SMS) with a click.We sent you!The option to cancel sending by email and mobile Will be available in the sent email.00:0003:03
60% CompleteSoon... -
Ophir BlogAffordable, sustainable laser welding and cutting
Manufacturers are turning to just-in-time production to meet the needs of complex, ever-changing supply chains. This ...
02:54Affordable, sustainable laser welding and cuttinghttp://summur.ai/lFYVYAffordable, sustainable laser welding and cuttingManufacturers are turning to just-in-time production to meet the needs of complex, ever-changing supply chains. This means the production process has to be extremely efficient – and smooth – with every component coming out just right.
For processes using laser cutting and welding, this involves using laser measurements to make sure the laser is interacting correctly with the materials being processed. For an efficient system, automated measurements are ideal – but these are often costly.
Let’s take a look at Ophir’s article, which highlights how laser cutting and welding processes can be kept running at maximum performance, while still being both affordable, and sustainable.
Quality problems are often the heart of component failure – slowing down production lines. Sadly, in many cases, quality control lags behind the advanced laser technologies. If systems are rarely tested, and outdated measurement systems are used – there’s a real risk of creating subpar products which would slow down the production lines and cause many unhappy customers.
Especially when it comes to the high power lasers used in industrial processes, tight tolerances must be met – and that can only be done if continuous beam profiling is performed.
If thermal changes occur, early awareness and preventative maintenance is key to making sure the finished components are not affected.
So, how can this be done without going over budget?
Ophir brings hope with its BeamWatch contactless measurement system, based on Rayleigh scattering – the scattering of electromagnetic waves by particles smaller than the radiation’s wavelength, such as oxygen or nitrogen molecules in the air. It can take real-time laser profiling measurements without touching the laser beam.The BeamWatch Integrated takes this once step further, as it can be integrated into automated production lines, for super efficient and high quality processes.
Not only are these systems affordable in themselves - but laser monitoring also saves money down the line – as any quality problems can be detected as early as possible, leading towards zero-defect production – perfect for efficient, just-in-time production lines.
And – as contactless measurement systems don’t touch the laser beams, they don’t degrade over time - - making them sustainable too, with no need for maintenance.
See the article to find out more about this incredible technology.
We just need your phone...After entering the number, the mobile send button will be available to you in all items.
Send to mobileAfter a short one-time registration, all the articles will be opened to you and we will be able to send you the content directly to the mobile (SMS) with a click.We sent you!The option to cancel sending by email and mobile Will be available in the sent email.00:0002:54
60% CompleteSoon... -
Ophir BlogTop tips for a damage-free thermal sensor
Did you know that a thermal sensor can be used for many years, without the need for a single repair?
Let&...
02:39Top tips for a damage-free thermal sensorDid you know that a thermal sensor can be used for many years, without the need for a single repair?
Let’s take a look at Ophir’s article on avoiding thermal sensor damage - and find out what expert technicians have to say about keeping your thermal sensors in top condition for years to come.
According to the experts, thermal sensor damage comes from incorrect laser optical setup and usage. The articles discusses the most common causes of incorrect usage, and preventative measures you can use to keep your thermal sensors in pristine condition.
First up – surface contamination. It’s very common for thermal sensors to get dirty. It’s important to find our the source of this contamination – and take measures to prevent it. For example, in the metalworking industry – welding too close to a sensor can easily contaminate it, and should be avoided.
Preventing sensor contamination is easy – clean the sensor regularly, use a protective housing, store it in a clean, closed container when not in use - and avoid touching it with your bare hands.
Another common cause of issues is overheating the sensor.
If you use your thermal sensor at power levels that are too high, for a long period of time, you’re likely to see damage to the absorber layer.
And – if your sensor is one that uses thermal grease for thermal coupling – you’ll start to see grease contamination too.
Always keep to the power range and power density threshold listed in the sensor’s specifications.Some high power sensors require water cooling. You should make sure the water you use meets quality requirements - otherwise it can cause significant damage.
Only deionized and filtered water should be used - the water should be clean, clear, and sediment free and for deionized water it’s also important to maintain a neutral pH level.
When it comes to a damaged sensor – it’s always worth getting it tested – some sensor damage is only cosmetic, and doesn’t affect the reliability of measurement results. Other forms of damage require full sensor disc replacement.
Take a look at the full article to see pictures of different types of sensor damage, and read more details about the measures you can take to keep your sensors in pristine condition.
We just need your phone...After entering the number, the mobile send button will be available to you in all items.
Send to mobileAfter a short one-time registration, all the articles will be opened to you and we will be able to send you the content directly to the mobile (SMS) with a click.We sent you!The option to cancel sending by email and mobile Will be available in the sent email.00:0002:39
60% CompleteSoon... -
Ophir BlogFighting viruses with UV-LEDs
Fighting viruses has been on everyone’s mind since the COVID-19 pandemic began. Let’s explore Ophir&rsquo...
02:23Fighting viruses with UV-LEDsFighting viruses has been on everyone’s mind since the COVID-19 pandemic began. Let’s explore Ophir’s article on how UV light can be used for this noble cause.
As early as the 19th century, we’ve known that viruses are sensitive to heat and UV light. But how can that knowledge be translated into something actionable in the fight against viruses like COVID-19?
Well, primarily, it’s good for disinfecting things. Usually, a place like a hospital would rely on harsh chemical disinfectants – but UV light is pretty good at it too.
There have been studies on different coronaviruses over the years that have proved that these viruses are indeed sensitive to UV-C light. As long as a high enough irradiation and irradiation period are used, coronaviruses can be curbed considerably.
UV light is indeed already used for hygiene purposes – to disinfect water and surfaces. Read the full article to find out more about the parameters needed to get this job done.
So, how do we get these UV rays in the first place? For a long time, mercury vapor lamps have been used to produce UV-C light and kill microorganisms, such as viruses. In future, UV-C LEDs might become more popular, as they have a long service life, can be dimmed, and their peak wavelengths can be adjusted.
Of course, the UV rays must be measured – to ensure safe and effective disinfection – what kind of measurements are needed? Intensity, dose, and the radiant power of divergent light sources, to name a few. Ophir’s various power and energy measuring devices and integrating spheres are well suited to this important task – click on the link in the article to see more details.
Only time – and lots of research - can tell us if UV-LEDs will help fight pandemics such as COVID-19. With Ophir’s measurement equipment, maybe we’ll get there that bit sooner!
We just need your phone...After entering the number, the mobile send button will be available to you in all items.
Send to mobileAfter a short one-time registration, all the articles will be opened to you and we will be able to send you the content directly to the mobile (SMS) with a click.We sent you!The option to cancel sending by email and mobile Will be available in the sent email.00:0002:23
60% CompleteSoon... -
Ophir BlogWhen laser measurements are a must for materials processing
“If you can’t measure it, you can’t improve it”. Those are the words first spoken by William ...
02:57When laser measurements are a must for materials processinghttp://summur.ai/lFYVYWhen laser measurements are a must for materials processing“If you can’t measure it, you can’t improve it”. Those are the words first spoken by William Thomson, a 19th century British physicist, also known as Lord Kelvin.
When it comes to improving laser-based processes, in the field of materials processing – these words certainly ring true.
Let’s explore Ophir’s article and find out how, and when, these measurements must absolutely, positively be made.
The way the laser light is applied to the material being processed is measured as a function of power density, or energy density. If the laser power or beam size change over time, the new power density will affect the way the laser light is applied to the material – causing unexpected results. This makes it extremely important to collect and apply laser measurement data at certain times in a laser’s lifecycle, to ensure the process is consistent.
The article lists five stages when laser measurement is essential.
One - during application development – as the precise implementation of key performance parameters will determine the productivity of the laser system.
Two - when the laser source is integrated in the system – at this point, the parameters of the developed application are usually transferred to a very similar laser for use in the actual system, so measurements should be retaken and compared, to ensure they remain the same.
Three - during system runoff, delivery and movement – before the system is accepted by the customer, to ensure it meets the required criteria.
Four – periodically during productive use, as components may degrade over time, and debris can collect, affecting performance.
And finally, five – for preventative and corrective maintenance – a comprehensive maintenance routine protects the laser. Measurements before and after the maintenance can validate the system’s performance.
Read the article to find out more about each of these stages.
Another important factor is the repeatability of the measurements – they must be reliable, and easy to perform, to ensure consistent results. One tool suited to this task is Ophir’s BeamWatch laser beam profiler – as it provides real-time, non-contact measurements, and is very simple to set up. Follow the link in the article for more information.
There’s no question that materials processing demands reliable and frequent laser measurements – throughout the laser’s lifetime – and luckily, Ophir offers tools to suit every system.
We just need your phone...After entering the number, the mobile send button will be available to you in all items.
Send to mobileAfter a short one-time registration, all the articles will be opened to you and we will be able to send you the content directly to the mobile (SMS) with a click.We sent you!The option to cancel sending by email and mobile Will be available in the sent email.00:0002:57
60% CompleteSoon... -
Ophir BlogHow Consistent Measuring Ensures the Quality of Medical Lasers
Over the past several years, the fields of aesthetic medicine, surgery and cosmetics have been revolutionized by ...
08:43How Consistent Measuring Ensures the Quality of Medical Lasershttp://summur.ai/lFYVYHow Consistent Measuring Ensures the Quality of Medical LasersOver the past several years, the fields of aesthetic medicine, surgery and cosmetics have been revolutionized by laser technology. With the development of their innovative laser systems, Asclepion Laser Technologies contributes greatly to patient well-being and faster healing. A consistent measurement strategy, effective testing processes and first-class measuring devices guarantee the high quality of the company's manufacturing at all times. For decades, Asclepion has relied on Ophir measuring technology from MKS Instruments to check the power and energy of the laser beam. To adjust it's PicoStar® laser, the company measures and analyzes the beam profile of this pico-second laser using an Ophir CCD camera combined with a beam reducer.
Asclepion Laser Technologies has been active in the area of international medical laser technology since 1977. The company's home base in the Jena Optical Valley promises – and delivers – extraordinary strength in innovation: The laser systems and their components are developed and manufactured almost entirely in-house. Over the past few years, the breadth of the company's portfolio has grown steadily; today it ranges from CO2 and solid-state lasers for dermatological and surgical procedures to diode lasers, for example for vascular applications and permanent hair removal. And it has expanded its offerings for the field of dermatology with the development of a picosecond laser: The PicoStar laser effectively and gently removes tattoos, permanent makeup and benign pigmentation.
A necessary condition for the great success of Asclepion Laser Technologies is the continued maintenance of strict quality standards. To this end, the company has developed a finely tuned measuring and testing process to which every laser system is subjected before being shipped. It rests on three essential pillars:
• Consistent measuring technology from development through to maintenance
• The right measuring technology for each application
• Meticulous quality inspection, based on the principle of double checksDuring production and, above all, during the final inspection of the laser systems, the measured parameters are continually compared against the specifications. To prevent influences due to measurement tolerances, calibrated systems of the same type are used to measure both prototypes still in development and finished laser systems before shipping or during commissioning or maintenance at the user's site.
When selecting a supplier, Roman Roth – process engineer at Asclepion and the person responsible for the proper and smooth running of manufacturing processes – has several prerequisites: "On the one hand, all our departments need reliable measurement equipment to provide us with accurate and repeatable results. At the same time, our wide range of laser types means that we need many different measurement methods. With MKS, we know that our demands – in terms of both the quality and the diversity of measurement solutions – can be met with standard Ophir sensors or individualized approaches" For example, to measure the power of an Asclepion diode laser, the company uses an MKS thermal sensor, such as the Ophir L50(300)A. The same measuring principle is also applied to solid-state lasers for surgery.
The pulsed solid-state lasers used in dermatology, on the other hand, are measured with pyroelectric sensors. Because of the high power and energy densities involved, Asclepion relies on Ophir sensors of the type PE50BF-DIFH-C, PE50- DIF-ER-C, which have integrated diffusers and thus higher damage thresholds. In order to meet the special requirements of medical technology, the sensors are also adjusted for specific wavelengths, e.g. calibrated to 2940 nm.
Asclepion's collection of metrological solutions for laser power and energy is rounded out with Ophir photodiode sensors. They measure the pilot beam systems that aim at the target in all solid-state lasers, the power of which is in the range of just a few mW. Depending on the area of application, Asclepion transmits the measurement data either via PC interfaces or directly to compact, handheld display devices.
No matter what measurement principle is applied, one thing is certain: Every single laser system that leaves Asclepion's production facility undergoes meticulous final testing. A final inspection protocol – encompassing some 25 to 60 A4 pages – is worked through step by step; depending on the laser system, this last evaluation can take a few days to a week. According to the principle of double checks, every product produced by Asclepion must be formally tested and finally approved by the Quality Assurance Department on the factory site before being shipped out to customers.
Introduced in 2019, the company's picosecond laser proved to be a particular challenge: In addition to the power and/ or energy of the laser beam, the beam profile must also be carefully checked and pre-adjusted on the optical bench during the final test. Here, Asclepion relies on the beam profile measurement taken by an Ophir CCD camera in combination with a beam reducer and the BeamGage or BeamMic analysis software. If, at the end of the beam path, the laser is ever to provide the optimal conditions as prescribed by the laser specifications, it must be carefully pre-adjusted in stages. For this purpose, the beam profile is recorded with the CCD camera at three different positions along the optical bench. These figures show the measurements of a correctly adjusted laser compared to that of a misaligned laser.
Without this camera-based measuring solution, it would be difficult and time-consuming to adjust the resonator on the optical bench. Too much divergence in the beam would lead to unwanted radiation of downstream optical components. Using the CCD camera saves considerable time and effort in this sensitive process while ensuring repeatable measurements of the beam profile. Also in his role as Asclepion's test equipment officer, Roman Roth is very satisfied with the collaboration: "The Ophir measuring devices work reliably and deliver reproducible results – both of which are essential in medical technology. In terms of sustainability, the quality and durability of the measurement technology are beyond reproach; we're still using our Ophir Nova display devices from 1996."
In general, the Ophir measuring instruments are in constant use at Asclepion Laser Technologies. Whether in the development phase of the laser systems, in the final test or during installation and maintenance at the customer: Any deviation from the specification is detected, and potential sources of error are eliminated immediately. In this manner, decoupling mirrors of poor quality or inhomogeneous laser crystals, for example, have been caught and rejected during final testing. Roman Roth is sure of one thing: "No matter which of our lasers it is, it's tested with at least one Ophir instrument." This makes it all the more important to regularly check the more than 100 sensors from Ophir that are currently employed throughout the various areas of Asclepion Laser Technologies. Every year, these instruments are calibrated according to specs in Ophir's European calibration laboratory in Darmstadt. This in turn guarantees the precise measurement of all Asclepion laser systems and thus their enduring quality, for the safety of operators and patients alike.
We just need your phone...After entering the number, the mobile send button will be available to you in all items.
Send to mobileAfter a short one-time registration, all the articles will be opened to you and we will be able to send you the content directly to the mobile (SMS) with a click.We sent you!The option to cancel sending by email and mobile Will be available in the sent email.00:0008:43
60% CompleteSoon... -
Ophir BlogDiaMonTech Develops Non-invasive Blood Glucose Monitor Using M-IR Lasers
More than 400 million people worldwide suffer from diabetes. For them, the ability to measure blood glucose levels ...
08:24DiaMonTech Develops Non-invasive Blood Glucose Monitor Using M-IR Lasershttp://summur.ai/lFYVYDiaMonTech Develops Non-invasive Blood Glucose Monitor Using M-IR LasersMore than 400 million people worldwide suffer from diabetes. For them, the ability to measure blood glucose levels non-invasively (without piercing the skin) would be an enormous relief. Thanks to a patented development by DiaMonTech AG, this dream could soon come true for many people. The technology, which uses an infrared quantum cascade laser, is already available as a desktop device. But a smartphonesized instrument is soon to follow. In order to achieve this miniaturization without loss of quality, it is necessary to detect even minute changes in the laser beam. DiaMonTech used the Ophir Pyrocam to measure and characterize all their laser developments.
Many non-invasive methods for measuring blood glucose have failed because they were not accurate enough: Glucose values in body fluids such as tears, saliva or sweat do not correlate sufficiently with glucose values in blood. The situation is different for skin fluid (interstitial fluid – ISF). Measurements taken on ISF at points with good blood supply correspond well to the actual amount of glucose in the blood. DiaMonTech was founded in 2015, after years of research at the Goethe University Frankfurt. On the basis of this research, the company has developed the first noninvasive blood glucose meter, obtaining CE approval as a medical device in 2019.
The D-Base – as the desktop device is called – works based on infrared spectroscopy, and specifically the principle of photothermic deflection. For this purpose, a quantum cascade laser radiates infrared pulses in wavelengths ranging between 8 and 11μm into the deeper skin layers. The pulses of these wavelengths pass through the sensor element and excite the glucose molecules to oscillate briefly, with the fast relaxation a small amount of heat is given off to the environment. At the skin surface this results in a minimal increase in temperature. In the sensor element, the thermal gradient causes a thermal lens effect. The test beam of a red laser diode is deflected by this thermal lens as it passes through the IRE. The deflection is measured by a position-sensitive photodiode; the device calculates the glucose concentration based on the deflection.
The measuring principle has now been proven in everyday clinical practice, and numerous tests show that the measurements provide reliable results. However, as Sergius Janik, COO at DiaMonTech, explains, shrinking the size of the measuring device is still a challenge: "Diabetes patients want fast and compact measurement technology that they can easily use at home and on the road. This is the focus of all our current research." Only a few manufacturers offer the tunable quantum cascade lasers that DiaMonTech uses for the D-Base. In order to reduce the overall size of the measuring device, the laser must be as small as possible. However, the specific parameters of the laser beam must not be affected by this reduction in size. Even the classic quantum cascade lasers used thus far must meet these specifications exactly.
In order to evaluate the quality of a given quantum cascade laser, the DiaMonTech laboratory conducts detailed measurements on all of them to answer the following questions:
• What does the laser beam profile look like?
• What is the output power of the laser?
• How divergent is the beam?
• What is the pulse repetition rate?
• What is the pulse-to-pulse stability and shape of the pulse?
• How large is the focal spot on the skin?In the company's early days, the team relied on the knifeedge technique for laser measurement to obtain the beam profiles. But because the number of measuring points required is large, it takes several hours to measure a laser beam this way. Had the company applied this method in the development of its new, compact blood glucose meter, it would have lost a lot of time – and still, the results would not have been precise enough. After in-depth research and conducting an array of tests in their own laboratories, the experts decided on the Ophir Pyrocam-III-HR-C-A-PRO. Using this high-resolution pyroelectric matrix camera, the beam profile of an infrared laser can be measured both quickly and reliably. For the application at DiaMonTech, the camera was individually calibrated to the appropriate signal level. The camera data is then evaluated with the BeamGage software. Output power, beam profile and beam divergence can be determined by the camera in just a few seconds. Sergius Janik explains: "The Ophir Pyrocam is our key measuring device for characterizing the laser beam, and we use it every day. We use it not only for developing new prototypes, but also for quality assessment and troubleshooting. As necessary, we also make the Pyrocam available to our development partners, so they can make precise and reliable adjustments."
Janik describes a concrete application as an example of the enormous time savings achieved by the Pyrocam. During a series of tests conducted by the DiaMonTech lab on a new laser, the engineers were unable to focus the beam. The power distribution of the beam was very irregular, but the cause was not obvious at first glance.
Only the images taken with the Pyrocam provided an explanation. Instead of the desired symmetrical Gaussian beam profile, the beam appeared strongly distorted.
These results showed that the collimating lens of the beam was out of adjustment, which may have occurred during shipment. The laser system was sent back to the manufacturer, the lens was re-adjusted, and then the Pyrocam measurements showed a uniform beam profile.
Another challenge that arises when developing a compact blood glucose meter is the different beam position for any given wavelength. To detect glucose in the skin, it is necessary to take measurements using a variety of wavelengths in the infrared range. But with a tunable laser, as soon as the wavelength is changed, the beam moves (a.k.a. "beam hopping"). As a result, it enters the skin at a slightly different position (up to about ¼ mm) and – analogous to wrongly corrected vision – the thermal lens becomes blurred. When the DiaMonTech team changes the wavelengths, they use the Pyrocam to measure the focus position, which is marked with crosshairs. The BeamGage software records the changes in crosshair position for accurate tracking. The wavelengths that provide the most precise measurements can then be determined, based on the findings from these readings.
Faster measurements mean more efficient development:
Along the road to miniaturization in non-invasive blood glucose monitoring, there is no way around a camerabased measurement of the beam profile. Before purchasing a measuring device, DiaMonTech tested the solutions available on the market. The Ophir measuring device not only had a wavelength range suited to the purpose, it also provided the required performance range and offered very good value for the money. Janik appreciates the measurement technology: "The Pyrocam makes our daily work easier. We no longer waste hours on time-consuming measurements; rather, we get reliable results very quickly. This allows us to concentrate on the essential work of development."We just need your phone...After entering the number, the mobile send button will be available to you in all items.
Send to mobileAfter a short one-time registration, all the articles will be opened to you and we will be able to send you the content directly to the mobile (SMS) with a click.We sent you!The option to cancel sending by email and mobile Will be available in the sent email.00:0008:24
60% CompleteSoon... -
Ophir BlogGet your laser measurement ‘content fix’ on the go with Playter!
For over a decade, our team of experts in Ophir photonics has been creating super valuable professional content (...
02:55Get your laser measurement ‘content fix’ on the go with Playter!http://summur.ai/lFYVYGet your laser measurement ‘content fix’ on the go with Playter!For over a decade, our team of experts in Ophir photonics has been creating super valuable professional content (articles, white papers, blog posts, webinars) which was brought to you on a weekly basis on our blog and social media channels.
Our goal is simple. Bring you the best updates, technical tips and industry news that are relevant to your daily work. Why? again, simple – We care about your success.
We want you to perform your best not only through using our top products, but also through our experts’ knowledge and tips. This is why we work tirelessly to provide you with fresh professional content each week.
It’s clear – Our readers and followers are our biggest asset.
Over the last few years something has changed.Content overloading and lack of time makes it harder for us to read thoroughly and find time to consume the information we are interested in.While text has been around us for quite a while, audio showed up recently – offering the opportunity to stay up-to-date and learn while on the go.
As you know, one of Ophir’s most important values is to stay ahead and bring you the latest technologies and innovative solutions out there, not only in laser measurement but also in content consumption.
Therefore, we decided to make it easier for you to consume our content and take a step forward into audio.
As written in the Summurai blog, “Audio opens the door to a new type of communication — one that is adapted to all types of devices, and which can fit into even the smallest parts of everyone’s timeline.”
It’s time to Meet Playter®. Thanks to our new collaboration with Summurai we can now offer you the best of Ophir’s content summarized & read to you out loud.
The Playter allows you to choose whether you’d like to read our content or listen to it, now or later, to make it easy for you to get your knowledge whenever and wherever works for you.
From now on, you’ll be able to enjoy Ophir’s most popular blog posts, white papers and articles in a more convenient way, while driving, shopping or walking your dog.
Soon, you’ll be able to create your own playlist and even share it with colleagues through social media. How awesome is that?!
You’ll be able to find our audio content on the right side bar on our blog!If you like it or want to share any comments, we’ll be more than happy to hear.
Let us know what you think and which content you’d like us to Playter for you!We just need your phone...After entering the number, the mobile send button will be available to you in all items.
Send to mobileAfter a short one-time registration, all the articles will be opened to you and we will be able to send you the content directly to the mobile (SMS) with a click.We sent you!The option to cancel sending by email and mobile Will be available in the sent email.00:0002:55
60% CompleteSoon... -
Ophir BlogThings to remember before setting up your laser measurement equipment for the first time
It can be overwhelming to figure out how to set up your laser measurement system for the first time.
Let&...
02:46Things to remember before setting up your laser measurement equipment for the first timehttp://summur.ai/lFYVYThings to remember before setting up your laser measurement equipment for the first timeIt can be overwhelming to figure out how to set up your laser measurement system for the first time.
Let’s take a look at an article in which John McCauley, a Bus Dev manager at Ophir, revisits a product demonstration in which he had to confidently set up equipment to show a prospective customer. He used this experience to come up with a list of things to remember before setting up your equipment for the first time.
Before you even choose your equipment, it’s crucial to understand how your laser works.
Every laser has difference characteristics – is it continuous wave, or pulsed, for example. What is its power, energy, wavelengths?
How are you going to use the laser? What’s the application, and what does that mean for the laser?
If you’re using it for materials processing, you’re like to have a laser light coming out of a processing head, converging on a focused spot – the amount of light and the size of the focus spot are important things to know.
Once you understand your laser, it’s time to understand the whole laser system. Many times a measurement system is chosen after a laser system has already been designed and commissioned, so it has to fit in with the system and its limitations.
There are some characteristics that can create new challenges – glovebox welding lasers, for example, have a processing head at an offset, and a beam profiling system would need to be set up with this in mind.
The last thing you must remember is to know your measurement product limitations. Whatever happens - you mustn’t exceed your measurement product’s rated damage threshold by applying to high a power density. Measurements don’t need to be taken at the focus, where power density is highest – as laser power or energy will be the same whatever the beam size. The smaller the beam size, the higher the power density, the more chance of exceeding the measurement equipment damage threshold – which is not good for the equipment, or the measurements you’re taking.
Well armed with knowledge about your laser, laser system, and the laser measurement tools being used – setting up your laser system will be far less daunting.
Read the article for more details about this important information.
We just need your phone...After entering the number, the mobile send button will be available to you in all items.
Send to mobileAfter a short one-time registration, all the articles will be opened to you and we will be able to send you the content directly to the mobile (SMS) with a click.We sent you!The option to cancel sending by email and mobile Will be available in the sent email.00:0002:46
60% CompleteSoon... -
Ophir BlogA beginner’s guide to laser power measurement
If you’re a serious laser user, you’ll know how important it is to measure certain laser parameters. Of ...
02:45A beginner’s guide to laser power measurementIf you’re a serious laser user, you’ll know how important it is to measure certain laser parameters. Of those parameters, laser power is the most simple way to understand your laser. With the help of Ophir’s blog post – the beginner’s guide to laser power measurement, let’s talk about the first step in setting up a laser power measurement system – choosing the tools you’re going to use – the meter, or interface, and the sensor.
The meter, or interface, measures electric current, and displays the result. Ophir has a whole range of meters and PC interfaces, to suit any setup. There’s a link to the full list in the blog post.
Then – there’s the more complex choice – the sensor itself. The sensor must measure laser power accurately, and convert it to electric current – as that’s what the meter, or interface, reads.
If you’re looking for an easy way to make this choice – you’re in luck. There’s a link in the blog post to Ophir’s sensor finder, which allows you to enter your laser’s parameters and find the ideal sensor for your system.
What’s going on behind-the-scenes to generate these ‘best matches’?
Well, to start off with, there are two types of sensors to choose from – photodiodes, or thermopiles. What’s the difference?
If you have a low power laser, you’ll need a photodiode-based sensor, known as a PD sensor – for one simple reason – it’s the only type sensitive enough to measure lower power lasers.And conversely, a thermopile-based sensor, or thermal sensor, is less sensitive, but can measure far higher powers – making it the choice for high power lasers.
When it comes to lasers with continuous wave beams, there are three crucial parameters that need to be considered, for either type of sensor.
First, the sensor must be able to cover the wavelength used by your laser. Secondly, the sensor must work well for your laser’s power range. And finally, it must be the right diameter, so that it can fit into the laser aperture.
For pulsed beams, things get a bit more complicated, but that’s a story for another day.
We just need your phone...After entering the number, the mobile send button will be available to you in all items.
Send to mobileAfter a short one-time registration, all the articles will be opened to you and we will be able to send you the content directly to the mobile (SMS) with a click.We sent you!The option to cancel sending by email and mobile Will be available in the sent email.00:0002:45
60% CompleteSoon... -
Ophir BlogA complete toolkit for measuring and testing VCSELs
A VCSEL – a Vertical Cavity Surface Emitting Laser – is a semiconductor laser diode that can be packaged ...
02:58A complete toolkit for measuring and testing VCSELshttp://summur.ai/lFYVYA complete toolkit for measuring and testing VCSELsA VCSEL – a Vertical Cavity Surface Emitting Laser – is a semiconductor laser diode that can be packaged as hundreds of emitters on a single chip. This makes it useful for a whole range of applications – including face recognition, proximity sensors, and augmented reality displays – all features you may well find on your smartphone. To maximize device battery life, it’s crucial to measure VCSEL power consumption, and keep it low.
However, testing and a measuring a VCSEL has its challenges – the beams can be very wide, and are often used in pulsed mode.
Let’s dive into Ophir’s article, which explains the tools you need to measure VCSELs, despite these challenges.First up – power consumption.
An integrating sphere is used for collecting light at high angles, often with a suitable port adapter to support the VCSEL’s wide beam angles. The sphere is coupled with a photodiode detector, which can measure even the lowest power lasers – down to under 1 microwatt!You can also add other tools, such as spectrometers, to the sphere - and take multiple measurements at once.
For power levels above 100 milliwatts, you could choose a thermophile sensor instead - these are more compact and easy to use than integrating spheres.
Next - If the VCSEL is operating in pulsed mode - you may need to measure the energy per laser pulse – this can be done using pyroelectric and photodiode energy sensors.
For analyzing laser beam size, quality, shape, and divergence - beam profiling is essential. This is best done using a suitable camera, with Ophir’s BeamGage software for analysis. Why a camera? It’s the ideal way to get real-time, accurate measurements of the laser beam profile. See the article to find out about different methods for VCSEL beam profiling.
When it comes to measuring pulse shape and noise, you’ll need a high speed photodiode detector, which can be attached to an integrating sphere, or used in free space. Pair it with analysis in either the time or frequency domain.
Often, laser system manufacturers build measurement capabilities into their laser systems – Ophir offers these OEM solutions - to provide robust laser performance analysis and fast feedback for system control.
Visit the full article to read about Ophir’s VCSEL measurement solutions in further detail.
We just need your phone...After entering the number, the mobile send button will be available to you in all items.
Send to mobileAfter a short one-time registration, all the articles will be opened to you and we will be able to send you the content directly to the mobile (SMS) with a click.We sent you!The option to cancel sending by email and mobile Will be available in the sent email.00:0002:58
60% CompleteSoon... -
Ophir BlogLet’s get started with laser beam profiling
We’d all like it if lasers always worked as they were supposed to – but that’s not always the case...
02:57Let’s get started with laser beam profilingWe’d all like it if lasers always worked as they were supposed to – but that’s not always the case. So, like any process, we need some kind of process control – with lasers, you’ll want to be taking accurate measurements.
You might think measuring laser power is enough – but that leaves a lot of the story untold. Instead, laser beam profiling gives you more insight. Let’s explore Ophir’s blog post, and discover how to get started with laser beam profiling.
Let’s imagine a laser as a perfect, idealized beam of light – if something goes wrong, you’ll tweak the power and it will be fixed – right? Unfortunately, it’s not so simple. Lasers degrade with time, and that can change the beam’s spot and shape.
Increasing the beam’s power could even make the shape worse.
Beam profiling is the secret to monitoring laser beam size and shape, to ensure that the beam continues to look and behave exactly as designed.
So, how do you get started in implementing a profiling solution? First, you need to choose the right equipment – and to do that, you need to decide the measurements you’re planning to take. This could include beam width, overall beam shape, ellipticity, and M-squared – the beam quality factor. Most beam parameters are based on these measurements.
Then, it’s time to choose a beam profiler. Most profilers measure beam width – but in different ways. There’s a link in the blog post that explains this further.
Scanning slit profilers take tiny samples of the beam through two narrow slits, creating two one-dimensional profiles on the X-axis and Y-axis. You can use these to create a two dimensional image, but that doesn’t provide a full picture.
CCD cameras can product a full two dimensional image of the laser. But, they require that high power lasers have more attenuation, which can be a hassle. And very small lasers, such as those that are tens of microns, might do better with scanning slits - for higher resolution.
Both scanning slits and CCD cameras can be used to measure ellipticity and M-squared, although M-Squared requires the addition of an optical rail or mirror system to make measurements at multiple locations.
If you’re not sure where to start - visit the blog post and click on the link at the bottom to talk to an Ophir expert.
We just need your phone...After entering the number, the mobile send button will be available to you in all items.
Send to mobileAfter a short one-time registration, all the articles will be opened to you and we will be able to send you the content directly to the mobile (SMS) with a click.We sent you!The option to cancel sending by email and mobile Will be available in the sent email.00:0002:57
60% CompleteSoon... -
Ophir BlogThe alarming shortage of semiconductor chips
As part of a series of blog posts on future trends, Ophir, an MKS company, has raised awareness of an alarming ...
03:01The alarming shortage of semiconductor chipsAs part of a series of blog posts on future trends, Ophir, an MKS company, has raised awareness of an alarming concern – the worldwide shortage of semiconductor chips. These chips are used everywhere – from phones, laptops, and PCs – through to vehicles, washing machines, ATMs, and more.
Let’s find out how this shortage came about, what effects it is having on our world, and see how key players are stepping in to resolve it.
Like many of today’s issues, the trigger behind the semiconductor shortage was the COVID-19 pandemic.
During the pandemic, demand for laptops and computers surged. But this shortage didn’t just affect the production of personal computers, it also had a knock-on effect on other industries.
For example, a new car build typically contains up to 1500 different semiconductor chips. Delivery lead times for chips have gone from an average of 9 weeks, to a staggering 22 weeks.
The result? Delays in the production of over 1 million vehicles in North America alone, with worldwide manufacturers projected to lose about 210 billion dollars in sales.
In China, chip supply chain disruptions caused electricity shortages, leading the government to introduce rationing, ordering factories to work less hours per day. And yes, this has caused Chinese chip manufacturers to reduce their production, creating a catch-22 situation, where the chip shortage is getting harder to resolve.
With these issues creating havoc worldwide, key players have stepped in to assist. Among them - Intel has invested 20 billion dollars in two huge new semiconductor fabrication plants in Arizona.
Samsung Electronics has planned to triple their production capacity by 2026. And TSMC, the largest contract chipmaker in the world, have joined forces with Sony to invest 7 billion dollars in creating a factory in Japan.
Other companies are also ramping up production – SK Hynix, Micron Technology, Bosch, and Hyundai. You can read more about their efforts in the original blog post.
As key suppliers of semiconductor components, MKS also has an important role to play – and is well positioned to support these ongoing industry-wide efforts to increase production.
It’s our hope that with a joint effort, these companies will be able to mitigate the supply chain disruptions that we see today, and get semiconductor production back on track.
We just need your phone...After entering the number, the mobile send button will be available to you in all items.
Send to mobileAfter a short one-time registration, all the articles will be opened to you and we will be able to send you the content directly to the mobile (SMS) with a click.We sent you!The option to cancel sending by email and mobile Will be available in the sent email.00:0003:01
60% CompleteSoon... -
Ophir BlogThe secret to speedy laser process development
Anyone involved in automotive manufacturing knows how crucial it is to be able to weld efficiently and accurately. ...
02:51The secret to speedy laser process developmentAnyone involved in automotive manufacturing knows how crucial it is to be able to weld efficiently and accurately. Especially when laser seam welding sheets of zinc-coated steel, a common occurrence in the industry, there are many challenges – as these metals have disparate melting and evaporation properties.
Let’s explore this case study, which shows how Volkswagen’s team of experts in Wolfsburg took on an exciting research project – to develop a new and unique multi-focal laser welding process.
Project leader and engineer Alexander Franz immediately recognized the importance of measurement technologies in laser process development. The time taken to measure a laser has a direct effect on the overall process development time. To speed up development – the team chose Ophir’s BeamWatch laser measurement instrument.
The idea behind multi-focal laser welding is that several laser beams are generated at once by a laser beam optic, to join hot-dip galvanized sheets in a zero-gap configuration. Using two highly focused forward laser beams, and one welding spot, two and three sheet metal joints can be produced with extremely high seam quality.
What the secret to this impressive result? Keeping the geometry of the laser beams completely in sync – and to do that, you need to measure them. You can read the full case study to find out more about the types of measurements taken.
Ophir’s BeamWatch has unique properties which made it suited for this task – it measures the laser beams without touching them, and allows multiple beams to be measured at once.
Each measurement could be taken and displayed in less than 400 milliseconds. This is a massive improvement when compared to the five minutes or more it would take for each measurement, when using other measurement instruments.
In effect, with the BeamWatch, the team was able to see the results of every tiny change they made to the process in real time. Thanks to this – they developed and refined the new welding process very quickly.
Of course, the automotive industry is not the only application the BeamWatch is suited to – it’s compact, flexible, and easy to set up – making it ideal for troubleshooting and laser process development in any field.
We just need your phone...After entering the number, the mobile send button will be available to you in all items.
Send to mobileAfter a short one-time registration, all the articles will be opened to you and we will be able to send you the content directly to the mobile (SMS) with a click.We sent you!The option to cancel sending by email and mobile Will be available in the sent email.00:0002:51
60% CompleteSoon... -
Ophir BlogHow we found the right beam profiling solution for a nuclear-powered US Army submarine
The right beam for a super specific and complex military challenge
02:42How we found the right beam profiling solution for a nuclear-powered US Army submarinehttp://summur.ai/lFYVYHow we found the right beam profiling solution for a nuclear-powered US Army submarineHow we found the right beam profiling solution for a nuclear-powered US Army submarine
This case study follows the journey of the Ophir team, as they worked tirelessly to find the right beam profiling solution for a nuclear-powered submarine.
You’ll find out the winning combination of technologies, tools, and techniques that were used to carry out this challenging task.
The US Army embraces emerging technologies – and so, the Ophir team ended up looking into laser measurements for a laser in the periscope of a 6800 ton, nuclear-powered submarine.Of course, as with any military application, there are strict requirements to meet. In this case, the laser had to be extremely accurate.
As you can imagine, there are few things more challenging than ensuring high laser accuracy on a moving, underwater vehicle.
This laser operates in conditions with limited inputs - GPS data, and the influence of gravity on its orientation and alignment.
As a result, the quality of the laser beam - and its shape, size, and intensity - all become critical - and beam alignment must be measured with extremely high accuracy.Finding the right instrumentation for these measurements wasn’t easy!
After several attempts, the Ophir team discovered a winning combination - Ophir-Spiricon BeamGage software, together with the Spiricon SP300 - a high-speed, high-resolution USB3 CCD camera.
Three key measurements were taken - a baseline source beam measurement, the beam’s ellipticity, and the laser source’s Gaussian Fit.
Next, these measurements were repeated at greater distances from the source, to calculate changes, and see if these changes were within tolerance. This method allowed them to capture both qualitative and quantitative differences, so the source could be improved and adjusted.
The beam profiling software proved itself vital for capturing the measurements and images needed. This data was used to identify the critical variables, from both the laser source and the final assembly, which would have an impact on the system.
With the right technologies, techniques, and tools - the team was able to ensure maximum laser system performance for this challenging underwater military application.
Take a look at the original case study – where you’ll see some of the measurements captured, in their graphical form.
Dick RieleyEast Coast Regional Sales Manager, Ophir Photonics GroupWe just need your phone...After entering the number, the mobile send button will be available to you in all items.
Send to mobileAfter a short one-time registration, all the articles will be opened to you and we will be able to send you the content directly to the mobile (SMS) with a click.We sent you!The option to cancel sending by email and mobile Will be available in the sent email.00:0002:42
60% CompleteSoon...
-
Ophir by MKS
Ophir Power/Energy Meter Calibration Procedure
02:37Ophir Power/Energy Meter Calibration ProcedureWhen it comes to laser measurement systems, accuracy is super important. A world-leader like Ophir uses strict processes to ensure measurement accuracy and analyze – and quantify - calibration errors. Let’s look at Ophir’s article and see how they’re making sure their laser power and energy meters meet specifications.
The total accuracy of measurement is influenced by many different factors – such as wavelength, sensor linearity, uniformity of readings over the surface, pulse rate, display unit calibration uncertainty, damage done to the absorber surface, and electromagnetic interference. The article describes all of these factors, and how they are handled when it comes to Ophir sensors – read the article in full to find out more.
The article primarily discusses two factors – firstly – the power calibration uncertainty of the measuring sensor at the power level, energy level, and wavelength at which it was calibrated, and secondly - the energy calibration uncertainty – this is the extra error due to the extra calibration step needed to calibrate energy.
Ophir’s accuracy specifications are in general “2 Sigma”. This means that, statistically, in 95% of cases the error of the system measured will not exceed the stated error. For example, if the stated error is plus minus 3 percent, then in 95% of cases, it will not exceed 3%, and in 99% of cases, it will not exceed 4%.
Ophir goes to great lengths to ensure sensors are calibrated to meet strict requirements. The possible errors are analyzed using advanced statistical techniques, resulting in highly accurate and reliable specifications. This is done for all types of sensors, and the article outlines the exact calculations made, as well as the resulting expected error, for each type of Ophir measurement device.
If you’re interested in knowing all of the hard work that goes into ensuring that Ophir’s high quality laser measurement devices have accurate specifications and minimal total error, be sure to check out the article.
We just need your phone...After entering the number, the mobile send button will be available to you in all items.
Send to mobileAfter a short one-time registration, all the articles will be opened to you and we will be able to send you the content directly to the mobile (SMS) with a click.We sent you!The option to cancel sending by email and mobile Will be available in the sent email.00:0002:37
60% Complete -
Ophir by MKS
So you want to convert a laser wavelength?
03:22So you want to convert a laser wavelength?The wavelength of a laser is one of its fundamental characteristics. Laser diodes, one of the most common laser sources, have wavelengths determined by their design and the materials they are made from. But what happens when you need a specific wavelength for your application, and the laser can’t generate it? That’s where laser wavelength conversion is used. Let’s take a look at Ophir’s article and find out how this is done.
First, let’s talk about tuneable lasers. Some lasers can be tuned, although the tuning range is limited by the gain medium bandwidth. The tuning is done by controlling loss in the laser cavity so it’s minimized for the wavelength at which lasing occurs. Tuning mechanisms can include controlling the laser’s temperature, or using microelectromechanical actuators to change the cavity’s length.
Most solid state lasers are not tuneable, as they have a narrow gain spectrum. One exception is the Ti-Sapphire laser which has a wide gain bandwidth and can be tuned between 650-1100 nanometers.
Linear wavelength conversion involves using the laser to pump a gain medium, such as a crystal, to a higher energy state – and the excited electrons then decay to a lower energy state by emitting radiation at a longer wavelength. Put the gain medium in a cavity, and a laser is formed. An example is the Nd-YAG laser, which is pumped by a laser diode at 808 nanometers and emits radiation at 1064 nanometers.
Next, we have nonlinear wavelength conversion, such as second-harmonic generation (SHG). A well-known example is the green laser that that uses a nonlinear crystal to convert 1064 nanometers to 532 nanometers. There are many requirements involved in this type of conversion, such as meeting phase matching conditions – read the article to find out more.
Lastly, we have non-coherent laser-driven light sources. One example is the generation of plasma that emits extreme ultraviolet radiation at a wavelength of 13 nanometers. This plasma is generated by focusing a high power CO2 laser, with a wavelength of about 10 micrometers, onto tin droplets in a vacuum – resulting in EUV light that enables advanced photolithography in the microelectronics industry. Read more about it in the article.
So, to round it up – it’s not always possible to get the wavelength you need for a specific application, due to limitations in the laser and in the materials and processes involved. But, nonlinear optical elements can allow the laser industry to reach further into more wavelength regions, enabling processes that are otherwise impossible to attain.
We just need your phone...After entering the number, the mobile send button will be available to you in all items.
Send to mobileAfter a short one-time registration, all the articles will be opened to you and we will be able to send you the content directly to the mobile (SMS) with a click.We sent you!The option to cancel sending by email and mobile Will be available in the sent email.00:0003:22
60% Complete -
Ophir by MKS
Measurement tools? Lasers are leading the way
03:12Measurement tools? Lasers are leading the wayLasers are used in so many ways, from optical fiber internet to performing sophisticated medical procedures. But they’re also superstars in another field – measurements. Let’s explore Ophir’s article on lasers as measurement tools.
Laser-assisted measurements can enhance and improve the way physical quantities are measured. They can calculate the distance between objects, using different methods depending on the size of the object, it’s distance from the measurement device, and the required resolution.
For example, there’s LiDAR – which encompasses a range of techniques for generating 3D maps of the environment, based on projecting laser light and detecting the reflected signal. It’s often used for autonomous vehicle navigation, to determine the best and safest driving strategy.
Lasers have been useful in other fields of measurement – such as interferometry, spectroscopy, microscopy, and atomic clocks.
Interferometry relies on superimposing electromagnetic radiation that has traversed different optical paths, and extracting information from the resulting interference pattern. The world’s most advanced interferometer stands in the heart of the Laser Interferometer Gravitational-Wave Observatory experiment. It can detect gravitational waves due to the change they exert on a laser beam that travels in one of its four-kilometer-long interferometer arms, measuring changes in optical path of less than one ten thousandth of the size of a proton! Read the article to find out more.
Spectroscopy is the study of interaction between light and matter – a laser with a well-defined wavelength can be used to investigate energy gaps between two electronic states of atoms or molecules. This technology has allowed scientists to catalog atomic and molecular transitions of almost every element and molecule known to us.
Microscopy is the use of microscopes to magnify objects. At first, microscopes used only lenses to view the object with visible light, and their maximum resolution was limited by diffraction due to the wave nature of light. But super-resolution microscopes, using lasers, have found ways to surpass the diffraction limit, with incredible results.
Lastly – lasers play a key role in atomic clocks – the most precise time-measurement system device built by man. Atomic clocks use the known energy-level differences of certain atoms to generate a highly stable and repeatable signal, with a known frequency - from which time can be measured. Read the article to find out more about the laser’s involvement in this fascinating application.
All in all, lasers have contributed greatly to developing measurement tools that go above and beyond the capabilities of other measurement technologies.
We just need your phone...After entering the number, the mobile send button will be available to you in all items.
Send to mobileAfter a short one-time registration, all the articles will be opened to you and we will be able to send you the content directly to the mobile (SMS) with a click.We sent you!The option to cancel sending by email and mobile Will be available in the sent email.00:0003:12
60% Complete -
Ophir by MKS
A journey through the evolution of man-made light sources
03:03A journey through the evolution of man-made light sourcesSince the beginning of time, man had busied itself with creating light sources. Let’s travel through time using Ophir’s article to explore the man-made light sources of the past, present, and future.
The earliest light sources were of course fire-based. The humble fire served as a light source, but also provided heat for cooking and warmth. Then, candles and oil lamps allowed fire to be controlled just for the purpose of providing light.
Moving on to the beginning of the 19th century, gas lanterns appeared in the streets of major European and American cities.
At the end of the 19th century, the incandescent light bulb made its first appearance – the rise of the electric light. 140 years later, we still use these bulbs. However, there are some problems – with electric current transmitting through a highly-resistant filament, only a very small portion of electrical energy is made into light – the rest is lost as unwanted heat. Also, much of the radiation produced is invisible, limiting the bulb’s luminous efficacy to 17 lumen/Watt.
So, what was next? Along came neon and fluorescent lights – using atomic transitions in gas tubes, triggered by electric discharge – leading to more durable and more energy-efficient light sources, with the ability to create bright white light. The downside? These light sources are fragile, and can contain hazardous elements. Their light also appears less natural due to spikes in their emission spectra.
Most recently, LED light sources have taken the forefront. Light Emitting Diodes are semiconductor light sources. In the 1960s, LEDs could only emit infrared, and then red, light – they were mainly used as indicators for electronic devices. It took more than 30 years to develop an LED light source that could be used for general purpose lighting – read the article to find out exactly how this was done.
The incandescent light bulb is expected to become history, thanks to LEDs, with their high luminous efficacy of 300 lumen/Watt and far longer lifetimes.
Are they perfect? Unfortunately not. There are concerns that the UV component of white light LEDs may be damaging to eyes and skin. And while the LED’s emission spectrum is smoother than that of neon or fluorescent lighting, and so its light looks more natural, it isn’t as smooth as the light generated by an incandescent light bulb. Constant research and development aims to improve LEDs even more, and we’re excited to see that happen.
Interested in hearing more? Read the full article.
We just need your phone...After entering the number, the mobile send button will be available to you in all items.
Send to mobileAfter a short one-time registration, all the articles will be opened to you and we will be able to send you the content directly to the mobile (SMS) with a click.We sent you!The option to cancel sending by email and mobile Will be available in the sent email.00:0003:03
60% Complete -
Ophir Blog
Affordable, sustainable laser welding and cutting
02:54Affordable, sustainable laser welding and cuttinghttp://summur.ai/lFYVYAffordable, sustainable laser welding and cuttingManufacturers are turning to just-in-time production to meet the needs of complex, ever-changing supply chains. This means the production process has to be extremely efficient – and smooth – with every component coming out just right.
For processes using laser cutting and welding, this involves using laser measurements to make sure the laser is interacting correctly with the materials being processed. For an efficient system, automated measurements are ideal – but these are often costly.
Let’s take a look at Ophir’s article, which highlights how laser cutting and welding processes can be kept running at maximum performance, while still being both affordable, and sustainable.
Quality problems are often the heart of component failure – slowing down production lines. Sadly, in many cases, quality control lags behind the advanced laser technologies. If systems are rarely tested, and outdated measurement systems are used – there’s a real risk of creating subpar products which would slow down the production lines and cause many unhappy customers.
Especially when it comes to the high power lasers used in industrial processes, tight tolerances must be met – and that can only be done if continuous beam profiling is performed.
If thermal changes occur, early awareness and preventative maintenance is key to making sure the finished components are not affected.
So, how can this be done without going over budget?
Ophir brings hope with its BeamWatch contactless measurement system, based on Rayleigh scattering – the scattering of electromagnetic waves by particles smaller than the radiation’s wavelength, such as oxygen or nitrogen molecules in the air. It can take real-time laser profiling measurements without touching the laser beam.The BeamWatch Integrated takes this once step further, as it can be integrated into automated production lines, for super efficient and high quality processes.
Not only are these systems affordable in themselves - but laser monitoring also saves money down the line – as any quality problems can be detected as early as possible, leading towards zero-defect production – perfect for efficient, just-in-time production lines.
And – as contactless measurement systems don’t touch the laser beams, they don’t degrade over time - - making them sustainable too, with no need for maintenance.
See the article to find out more about this incredible technology.
We just need your phone...After entering the number, the mobile send button will be available to you in all items.
Send to mobileAfter a short one-time registration, all the articles will be opened to you and we will be able to send you the content directly to the mobile (SMS) with a click.We sent you!The option to cancel sending by email and mobile Will be available in the sent email.00:0002:54
60% Complete -
Ophir Blog
Top tips for a damage-free thermal sensor
02:39Top tips for a damage-free thermal sensorDid you know that a thermal sensor can be used for many years, without the need for a single repair?
Let’s take a look at Ophir’s article on avoiding thermal sensor damage - and find out what expert technicians have to say about keeping your thermal sensors in top condition for years to come.
According to the experts, thermal sensor damage comes from incorrect laser optical setup and usage. The articles discusses the most common causes of incorrect usage, and preventative measures you can use to keep your thermal sensors in pristine condition.
First up – surface contamination. It’s very common for thermal sensors to get dirty. It’s important to find our the source of this contamination – and take measures to prevent it. For example, in the metalworking industry – welding too close to a sensor can easily contaminate it, and should be avoided.
Preventing sensor contamination is easy – clean the sensor regularly, use a protective housing, store it in a clean, closed container when not in use - and avoid touching it with your bare hands.
Another common cause of issues is overheating the sensor.
If you use your thermal sensor at power levels that are too high, for a long period of time, you’re likely to see damage to the absorber layer.
And – if your sensor is one that uses thermal grease for thermal coupling – you’ll start to see grease contamination too.
Always keep to the power range and power density threshold listed in the sensor’s specifications.Some high power sensors require water cooling. You should make sure the water you use meets quality requirements - otherwise it can cause significant damage.
Only deionized and filtered water should be used - the water should be clean, clear, and sediment free and for deionized water it’s also important to maintain a neutral pH level.
When it comes to a damaged sensor – it’s always worth getting it tested – some sensor damage is only cosmetic, and doesn’t affect the reliability of measurement results. Other forms of damage require full sensor disc replacement.
Take a look at the full article to see pictures of different types of sensor damage, and read more details about the measures you can take to keep your sensors in pristine condition.
We just need your phone...After entering the number, the mobile send button will be available to you in all items.
Send to mobileAfter a short one-time registration, all the articles will be opened to you and we will be able to send you the content directly to the mobile (SMS) with a click.We sent you!The option to cancel sending by email and mobile Will be available in the sent email.00:0002:39
60% Complete -
Ophir Blog
Fighting viruses with UV-LEDs
02:23Fighting viruses with UV-LEDsFighting viruses has been on everyone’s mind since the COVID-19 pandemic began. Let’s explore Ophir’s article on how UV light can be used for this noble cause.
As early as the 19th century, we’ve known that viruses are sensitive to heat and UV light. But how can that knowledge be translated into something actionable in the fight against viruses like COVID-19?
Well, primarily, it’s good for disinfecting things. Usually, a place like a hospital would rely on harsh chemical disinfectants – but UV light is pretty good at it too.
There have been studies on different coronaviruses over the years that have proved that these viruses are indeed sensitive to UV-C light. As long as a high enough irradiation and irradiation period are used, coronaviruses can be curbed considerably.
UV light is indeed already used for hygiene purposes – to disinfect water and surfaces. Read the full article to find out more about the parameters needed to get this job done.
So, how do we get these UV rays in the first place? For a long time, mercury vapor lamps have been used to produce UV-C light and kill microorganisms, such as viruses. In future, UV-C LEDs might become more popular, as they have a long service life, can be dimmed, and their peak wavelengths can be adjusted.
Of course, the UV rays must be measured – to ensure safe and effective disinfection – what kind of measurements are needed? Intensity, dose, and the radiant power of divergent light sources, to name a few. Ophir’s various power and energy measuring devices and integrating spheres are well suited to this important task – click on the link in the article to see more details.
Only time – and lots of research - can tell us if UV-LEDs will help fight pandemics such as COVID-19. With Ophir’s measurement equipment, maybe we’ll get there that bit sooner!
We just need your phone...After entering the number, the mobile send button will be available to you in all items.
Send to mobileAfter a short one-time registration, all the articles will be opened to you and we will be able to send you the content directly to the mobile (SMS) with a click.We sent you!The option to cancel sending by email and mobile Will be available in the sent email.00:0002:23
60% Complete -
Ophir Blog
When laser measurements are a must for materials processing
02:57When laser measurements are a must for materials processinghttp://summur.ai/lFYVYWhen laser measurements are a must for materials processing“If you can’t measure it, you can’t improve it”. Those are the words first spoken by William Thomson, a 19th century British physicist, also known as Lord Kelvin.
When it comes to improving laser-based processes, in the field of materials processing – these words certainly ring true.
Let’s explore Ophir’s article and find out how, and when, these measurements must absolutely, positively be made.
The way the laser light is applied to the material being processed is measured as a function of power density, or energy density. If the laser power or beam size change over time, the new power density will affect the way the laser light is applied to the material – causing unexpected results. This makes it extremely important to collect and apply laser measurement data at certain times in a laser’s lifecycle, to ensure the process is consistent.
The article lists five stages when laser measurement is essential.
One - during application development – as the precise implementation of key performance parameters will determine the productivity of the laser system.
Two - when the laser source is integrated in the system – at this point, the parameters of the developed application are usually transferred to a very similar laser for use in the actual system, so measurements should be retaken and compared, to ensure they remain the same.
Three - during system runoff, delivery and movement – before the system is accepted by the customer, to ensure it meets the required criteria.
Four – periodically during productive use, as components may degrade over time, and debris can collect, affecting performance.
And finally, five – for preventative and corrective maintenance – a comprehensive maintenance routine protects the laser. Measurements before and after the maintenance can validate the system’s performance.
Read the article to find out more about each of these stages.
Another important factor is the repeatability of the measurements – they must be reliable, and easy to perform, to ensure consistent results. One tool suited to this task is Ophir’s BeamWatch laser beam profiler – as it provides real-time, non-contact measurements, and is very simple to set up. Follow the link in the article for more information.
There’s no question that materials processing demands reliable and frequent laser measurements – throughout the laser’s lifetime – and luckily, Ophir offers tools to suit every system.
We just need your phone...After entering the number, the mobile send button will be available to you in all items.
Send to mobileAfter a short one-time registration, all the articles will be opened to you and we will be able to send you the content directly to the mobile (SMS) with a click.We sent you!The option to cancel sending by email and mobile Will be available in the sent email.00:0002:57
60% Complete -
Ophir Blog
How Consistent Measuring Ensures the Quality of Medical Lasers
08:43How Consistent Measuring Ensures the Quality of Medical Lasershttp://summur.ai/lFYVYHow Consistent Measuring Ensures the Quality of Medical LasersOver the past several years, the fields of aesthetic medicine, surgery and cosmetics have been revolutionized by laser technology. With the development of their innovative laser systems, Asclepion Laser Technologies contributes greatly to patient well-being and faster healing. A consistent measurement strategy, effective testing processes and first-class measuring devices guarantee the high quality of the company's manufacturing at all times. For decades, Asclepion has relied on Ophir measuring technology from MKS Instruments to check the power and energy of the laser beam. To adjust it's PicoStar® laser, the company measures and analyzes the beam profile of this pico-second laser using an Ophir CCD camera combined with a beam reducer.
Asclepion Laser Technologies has been active in the area of international medical laser technology since 1977. The company's home base in the Jena Optical Valley promises – and delivers – extraordinary strength in innovation: The laser systems and their components are developed and manufactured almost entirely in-house. Over the past few years, the breadth of the company's portfolio has grown steadily; today it ranges from CO2 and solid-state lasers for dermatological and surgical procedures to diode lasers, for example for vascular applications and permanent hair removal. And it has expanded its offerings for the field of dermatology with the development of a picosecond laser: The PicoStar laser effectively and gently removes tattoos, permanent makeup and benign pigmentation.
A necessary condition for the great success of Asclepion Laser Technologies is the continued maintenance of strict quality standards. To this end, the company has developed a finely tuned measuring and testing process to which every laser system is subjected before being shipped. It rests on three essential pillars:
• Consistent measuring technology from development through to maintenance
• The right measuring technology for each application
• Meticulous quality inspection, based on the principle of double checksDuring production and, above all, during the final inspection of the laser systems, the measured parameters are continually compared against the specifications. To prevent influences due to measurement tolerances, calibrated systems of the same type are used to measure both prototypes still in development and finished laser systems before shipping or during commissioning or maintenance at the user's site.
When selecting a supplier, Roman Roth – process engineer at Asclepion and the person responsible for the proper and smooth running of manufacturing processes – has several prerequisites: "On the one hand, all our departments need reliable measurement equipment to provide us with accurate and repeatable results. At the same time, our wide range of laser types means that we need many different measurement methods. With MKS, we know that our demands – in terms of both the quality and the diversity of measurement solutions – can be met with standard Ophir sensors or individualized approaches" For example, to measure the power of an Asclepion diode laser, the company uses an MKS thermal sensor, such as the Ophir L50(300)A. The same measuring principle is also applied to solid-state lasers for surgery.
The pulsed solid-state lasers used in dermatology, on the other hand, are measured with pyroelectric sensors. Because of the high power and energy densities involved, Asclepion relies on Ophir sensors of the type PE50BF-DIFH-C, PE50- DIF-ER-C, which have integrated diffusers and thus higher damage thresholds. In order to meet the special requirements of medical technology, the sensors are also adjusted for specific wavelengths, e.g. calibrated to 2940 nm.
Asclepion's collection of metrological solutions for laser power and energy is rounded out with Ophir photodiode sensors. They measure the pilot beam systems that aim at the target in all solid-state lasers, the power of which is in the range of just a few mW. Depending on the area of application, Asclepion transmits the measurement data either via PC interfaces or directly to compact, handheld display devices.
No matter what measurement principle is applied, one thing is certain: Every single laser system that leaves Asclepion's production facility undergoes meticulous final testing. A final inspection protocol – encompassing some 25 to 60 A4 pages – is worked through step by step; depending on the laser system, this last evaluation can take a few days to a week. According to the principle of double checks, every product produced by Asclepion must be formally tested and finally approved by the Quality Assurance Department on the factory site before being shipped out to customers.
Introduced in 2019, the company's picosecond laser proved to be a particular challenge: In addition to the power and/ or energy of the laser beam, the beam profile must also be carefully checked and pre-adjusted on the optical bench during the final test. Here, Asclepion relies on the beam profile measurement taken by an Ophir CCD camera in combination with a beam reducer and the BeamGage or BeamMic analysis software. If, at the end of the beam path, the laser is ever to provide the optimal conditions as prescribed by the laser specifications, it must be carefully pre-adjusted in stages. For this purpose, the beam profile is recorded with the CCD camera at three different positions along the optical bench. These figures show the measurements of a correctly adjusted laser compared to that of a misaligned laser.
Without this camera-based measuring solution, it would be difficult and time-consuming to adjust the resonator on the optical bench. Too much divergence in the beam would lead to unwanted radiation of downstream optical components. Using the CCD camera saves considerable time and effort in this sensitive process while ensuring repeatable measurements of the beam profile. Also in his role as Asclepion's test equipment officer, Roman Roth is very satisfied with the collaboration: "The Ophir measuring devices work reliably and deliver reproducible results – both of which are essential in medical technology. In terms of sustainability, the quality and durability of the measurement technology are beyond reproach; we're still using our Ophir Nova display devices from 1996."
In general, the Ophir measuring instruments are in constant use at Asclepion Laser Technologies. Whether in the development phase of the laser systems, in the final test or during installation and maintenance at the customer: Any deviation from the specification is detected, and potential sources of error are eliminated immediately. In this manner, decoupling mirrors of poor quality or inhomogeneous laser crystals, for example, have been caught and rejected during final testing. Roman Roth is sure of one thing: "No matter which of our lasers it is, it's tested with at least one Ophir instrument." This makes it all the more important to regularly check the more than 100 sensors from Ophir that are currently employed throughout the various areas of Asclepion Laser Technologies. Every year, these instruments are calibrated according to specs in Ophir's European calibration laboratory in Darmstadt. This in turn guarantees the precise measurement of all Asclepion laser systems and thus their enduring quality, for the safety of operators and patients alike.
We just need your phone...After entering the number, the mobile send button will be available to you in all items.
Send to mobileAfter a short one-time registration, all the articles will be opened to you and we will be able to send you the content directly to the mobile (SMS) with a click.We sent you!The option to cancel sending by email and mobile Will be available in the sent email.00:0008:43
60% Complete -
Ophir Blog
DiaMonTech Develops Non-invasive Blood Glucose Monitor Using M-IR Lasers
08:24DiaMonTech Develops Non-invasive Blood Glucose Monitor Using M-IR Lasershttp://summur.ai/lFYVYDiaMonTech Develops Non-invasive Blood Glucose Monitor Using M-IR LasersMore than 400 million people worldwide suffer from diabetes. For them, the ability to measure blood glucose levels non-invasively (without piercing the skin) would be an enormous relief. Thanks to a patented development by DiaMonTech AG, this dream could soon come true for many people. The technology, which uses an infrared quantum cascade laser, is already available as a desktop device. But a smartphonesized instrument is soon to follow. In order to achieve this miniaturization without loss of quality, it is necessary to detect even minute changes in the laser beam. DiaMonTech used the Ophir Pyrocam to measure and characterize all their laser developments.
Many non-invasive methods for measuring blood glucose have failed because they were not accurate enough: Glucose values in body fluids such as tears, saliva or sweat do not correlate sufficiently with glucose values in blood. The situation is different for skin fluid (interstitial fluid – ISF). Measurements taken on ISF at points with good blood supply correspond well to the actual amount of glucose in the blood. DiaMonTech was founded in 2015, after years of research at the Goethe University Frankfurt. On the basis of this research, the company has developed the first noninvasive blood glucose meter, obtaining CE approval as a medical device in 2019.
The D-Base – as the desktop device is called – works based on infrared spectroscopy, and specifically the principle of photothermic deflection. For this purpose, a quantum cascade laser radiates infrared pulses in wavelengths ranging between 8 and 11μm into the deeper skin layers. The pulses of these wavelengths pass through the sensor element and excite the glucose molecules to oscillate briefly, with the fast relaxation a small amount of heat is given off to the environment. At the skin surface this results in a minimal increase in temperature. In the sensor element, the thermal gradient causes a thermal lens effect. The test beam of a red laser diode is deflected by this thermal lens as it passes through the IRE. The deflection is measured by a position-sensitive photodiode; the device calculates the glucose concentration based on the deflection.
The measuring principle has now been proven in everyday clinical practice, and numerous tests show that the measurements provide reliable results. However, as Sergius Janik, COO at DiaMonTech, explains, shrinking the size of the measuring device is still a challenge: "Diabetes patients want fast and compact measurement technology that they can easily use at home and on the road. This is the focus of all our current research." Only a few manufacturers offer the tunable quantum cascade lasers that DiaMonTech uses for the D-Base. In order to reduce the overall size of the measuring device, the laser must be as small as possible. However, the specific parameters of the laser beam must not be affected by this reduction in size. Even the classic quantum cascade lasers used thus far must meet these specifications exactly.
In order to evaluate the quality of a given quantum cascade laser, the DiaMonTech laboratory conducts detailed measurements on all of them to answer the following questions:
• What does the laser beam profile look like?
• What is the output power of the laser?
• How divergent is the beam?
• What is the pulse repetition rate?
• What is the pulse-to-pulse stability and shape of the pulse?
• How large is the focal spot on the skin?In the company's early days, the team relied on the knifeedge technique for laser measurement to obtain the beam profiles. But because the number of measuring points required is large, it takes several hours to measure a laser beam this way. Had the company applied this method in the development of its new, compact blood glucose meter, it would have lost a lot of time – and still, the results would not have been precise enough. After in-depth research and conducting an array of tests in their own laboratories, the experts decided on the Ophir Pyrocam-III-HR-C-A-PRO. Using this high-resolution pyroelectric matrix camera, the beam profile of an infrared laser can be measured both quickly and reliably. For the application at DiaMonTech, the camera was individually calibrated to the appropriate signal level. The camera data is then evaluated with the BeamGage software. Output power, beam profile and beam divergence can be determined by the camera in just a few seconds. Sergius Janik explains: "The Ophir Pyrocam is our key measuring device for characterizing the laser beam, and we use it every day. We use it not only for developing new prototypes, but also for quality assessment and troubleshooting. As necessary, we also make the Pyrocam available to our development partners, so they can make precise and reliable adjustments."
Janik describes a concrete application as an example of the enormous time savings achieved by the Pyrocam. During a series of tests conducted by the DiaMonTech lab on a new laser, the engineers were unable to focus the beam. The power distribution of the beam was very irregular, but the cause was not obvious at first glance.
Only the images taken with the Pyrocam provided an explanation. Instead of the desired symmetrical Gaussian beam profile, the beam appeared strongly distorted.
These results showed that the collimating lens of the beam was out of adjustment, which may have occurred during shipment. The laser system was sent back to the manufacturer, the lens was re-adjusted, and then the Pyrocam measurements showed a uniform beam profile.
Another challenge that arises when developing a compact blood glucose meter is the different beam position for any given wavelength. To detect glucose in the skin, it is necessary to take measurements using a variety of wavelengths in the infrared range. But with a tunable laser, as soon as the wavelength is changed, the beam moves (a.k.a. "beam hopping"). As a result, it enters the skin at a slightly different position (up to about ¼ mm) and – analogous to wrongly corrected vision – the thermal lens becomes blurred. When the DiaMonTech team changes the wavelengths, they use the Pyrocam to measure the focus position, which is marked with crosshairs. The BeamGage software records the changes in crosshair position for accurate tracking. The wavelengths that provide the most precise measurements can then be determined, based on the findings from these readings.
Faster measurements mean more efficient development:
Along the road to miniaturization in non-invasive blood glucose monitoring, there is no way around a camerabased measurement of the beam profile. Before purchasing a measuring device, DiaMonTech tested the solutions available on the market. The Ophir measuring device not only had a wavelength range suited to the purpose, it also provided the required performance range and offered very good value for the money. Janik appreciates the measurement technology: "The Pyrocam makes our daily work easier. We no longer waste hours on time-consuming measurements; rather, we get reliable results very quickly. This allows us to concentrate on the essential work of development."We just need your phone...After entering the number, the mobile send button will be available to you in all items.
Send to mobileAfter a short one-time registration, all the articles will be opened to you and we will be able to send you the content directly to the mobile (SMS) with a click.We sent you!The option to cancel sending by email and mobile Will be available in the sent email.00:0008:24
60% Complete -
Ophir Blog
Get your laser measurement ‘content fix’ on the go with Playter!
02:55Get your laser measurement ‘content fix’ on the go with Playter!http://summur.ai/lFYVYGet your laser measurement ‘content fix’ on the go with Playter!For over a decade, our team of experts in Ophir photonics has been creating super valuable professional content (articles, white papers, blog posts, webinars) which was brought to you on a weekly basis on our blog and social media channels.
Our goal is simple. Bring you the best updates, technical tips and industry news that are relevant to your daily work. Why? again, simple – We care about your success.
We want you to perform your best not only through using our top products, but also through our experts’ knowledge and tips. This is why we work tirelessly to provide you with fresh professional content each week.
It’s clear – Our readers and followers are our biggest asset.
Over the last few years something has changed.Content overloading and lack of time makes it harder for us to read thoroughly and find time to consume the information we are interested in.While text has been around us for quite a while, audio showed up recently – offering the opportunity to stay up-to-date and learn while on the go.
As you know, one of Ophir’s most important values is to stay ahead and bring you the latest technologies and innovative solutions out there, not only in laser measurement but also in content consumption.
Therefore, we decided to make it easier for you to consume our content and take a step forward into audio.
As written in the Summurai blog, “Audio opens the door to a new type of communication — one that is adapted to all types of devices, and which can fit into even the smallest parts of everyone’s timeline.”
It’s time to Meet Playter®. Thanks to our new collaboration with Summurai we can now offer you the best of Ophir’s content summarized & read to you out loud.
The Playter allows you to choose whether you’d like to read our content or listen to it, now or later, to make it easy for you to get your knowledge whenever and wherever works for you.
From now on, you’ll be able to enjoy Ophir’s most popular blog posts, white papers and articles in a more convenient way, while driving, shopping or walking your dog.
Soon, you’ll be able to create your own playlist and even share it with colleagues through social media. How awesome is that?!
You’ll be able to find our audio content on the right side bar on our blog!If you like it or want to share any comments, we’ll be more than happy to hear.
Let us know what you think and which content you’d like us to Playter for you!We just need your phone...After entering the number, the mobile send button will be available to you in all items.
Send to mobileAfter a short one-time registration, all the articles will be opened to you and we will be able to send you the content directly to the mobile (SMS) with a click.We sent you!The option to cancel sending by email and mobile Will be available in the sent email.00:0002:55
60% Complete -
Ophir Blog
Things to remember before setting up your laser measurement equipment for the first time
02:46Things to remember before setting up your laser measurement equipment for the first timehttp://summur.ai/lFYVYThings to remember before setting up your laser measurement equipment for the first timeIt can be overwhelming to figure out how to set up your laser measurement system for the first time.
Let’s take a look at an article in which John McCauley, a Bus Dev manager at Ophir, revisits a product demonstration in which he had to confidently set up equipment to show a prospective customer. He used this experience to come up with a list of things to remember before setting up your equipment for the first time.
Before you even choose your equipment, it’s crucial to understand how your laser works.
Every laser has difference characteristics – is it continuous wave, or pulsed, for example. What is its power, energy, wavelengths?
How are you going to use the laser? What’s the application, and what does that mean for the laser?
If you’re using it for materials processing, you’re like to have a laser light coming out of a processing head, converging on a focused spot – the amount of light and the size of the focus spot are important things to know.
Once you understand your laser, it’s time to understand the whole laser system. Many times a measurement system is chosen after a laser system has already been designed and commissioned, so it has to fit in with the system and its limitations.
There are some characteristics that can create new challenges – glovebox welding lasers, for example, have a processing head at an offset, and a beam profiling system would need to be set up with this in mind.
The last thing you must remember is to know your measurement product limitations. Whatever happens - you mustn’t exceed your measurement product’s rated damage threshold by applying to high a power density. Measurements don’t need to be taken at the focus, where power density is highest – as laser power or energy will be the same whatever the beam size. The smaller the beam size, the higher the power density, the more chance of exceeding the measurement equipment damage threshold – which is not good for the equipment, or the measurements you’re taking.
Well armed with knowledge about your laser, laser system, and the laser measurement tools being used – setting up your laser system will be far less daunting.
Read the article for more details about this important information.
We just need your phone...After entering the number, the mobile send button will be available to you in all items.
Send to mobileAfter a short one-time registration, all the articles will be opened to you and we will be able to send you the content directly to the mobile (SMS) with a click.We sent you!The option to cancel sending by email and mobile Will be available in the sent email.00:0002:46
60% Complete -
Ophir Blog
A beginner’s guide to laser power measurement
02:45A beginner’s guide to laser power measurementIf you’re a serious laser user, you’ll know how important it is to measure certain laser parameters. Of those parameters, laser power is the most simple way to understand your laser. With the help of Ophir’s blog post – the beginner’s guide to laser power measurement, let’s talk about the first step in setting up a laser power measurement system – choosing the tools you’re going to use – the meter, or interface, and the sensor.
The meter, or interface, measures electric current, and displays the result. Ophir has a whole range of meters and PC interfaces, to suit any setup. There’s a link to the full list in the blog post.
Then – there’s the more complex choice – the sensor itself. The sensor must measure laser power accurately, and convert it to electric current – as that’s what the meter, or interface, reads.
If you’re looking for an easy way to make this choice – you’re in luck. There’s a link in the blog post to Ophir’s sensor finder, which allows you to enter your laser’s parameters and find the ideal sensor for your system.
What’s going on behind-the-scenes to generate these ‘best matches’?
Well, to start off with, there are two types of sensors to choose from – photodiodes, or thermopiles. What’s the difference?
If you have a low power laser, you’ll need a photodiode-based sensor, known as a PD sensor – for one simple reason – it’s the only type sensitive enough to measure lower power lasers.And conversely, a thermopile-based sensor, or thermal sensor, is less sensitive, but can measure far higher powers – making it the choice for high power lasers.
When it comes to lasers with continuous wave beams, there are three crucial parameters that need to be considered, for either type of sensor.
First, the sensor must be able to cover the wavelength used by your laser. Secondly, the sensor must work well for your laser’s power range. And finally, it must be the right diameter, so that it can fit into the laser aperture.
For pulsed beams, things get a bit more complicated, but that’s a story for another day.
We just need your phone...After entering the number, the mobile send button will be available to you in all items.
Send to mobileAfter a short one-time registration, all the articles will be opened to you and we will be able to send you the content directly to the mobile (SMS) with a click.We sent you!The option to cancel sending by email and mobile Will be available in the sent email.00:0002:45
60% Complete -
Ophir Blog
A complete toolkit for measuring and testing VCSELs
02:58A complete toolkit for measuring and testing VCSELshttp://summur.ai/lFYVYA complete toolkit for measuring and testing VCSELsA VCSEL – a Vertical Cavity Surface Emitting Laser – is a semiconductor laser diode that can be packaged as hundreds of emitters on a single chip. This makes it useful for a whole range of applications – including face recognition, proximity sensors, and augmented reality displays – all features you may well find on your smartphone. To maximize device battery life, it’s crucial to measure VCSEL power consumption, and keep it low.
However, testing and a measuring a VCSEL has its challenges – the beams can be very wide, and are often used in pulsed mode.
Let’s dive into Ophir’s article, which explains the tools you need to measure VCSELs, despite these challenges.First up – power consumption.
An integrating sphere is used for collecting light at high angles, often with a suitable port adapter to support the VCSEL’s wide beam angles. The sphere is coupled with a photodiode detector, which can measure even the lowest power lasers – down to under 1 microwatt!You can also add other tools, such as spectrometers, to the sphere - and take multiple measurements at once.
For power levels above 100 milliwatts, you could choose a thermophile sensor instead - these are more compact and easy to use than integrating spheres.
Next - If the VCSEL is operating in pulsed mode - you may need to measure the energy per laser pulse – this can be done using pyroelectric and photodiode energy sensors.
For analyzing laser beam size, quality, shape, and divergence - beam profiling is essential. This is best done using a suitable camera, with Ophir’s BeamGage software for analysis. Why a camera? It’s the ideal way to get real-time, accurate measurements of the laser beam profile. See the article to find out about different methods for VCSEL beam profiling.
When it comes to measuring pulse shape and noise, you’ll need a high speed photodiode detector, which can be attached to an integrating sphere, or used in free space. Pair it with analysis in either the time or frequency domain.
Often, laser system manufacturers build measurement capabilities into their laser systems – Ophir offers these OEM solutions - to provide robust laser performance analysis and fast feedback for system control.
Visit the full article to read about Ophir’s VCSEL measurement solutions in further detail.
We just need your phone...After entering the number, the mobile send button will be available to you in all items.
Send to mobileAfter a short one-time registration, all the articles will be opened to you and we will be able to send you the content directly to the mobile (SMS) with a click.We sent you!The option to cancel sending by email and mobile Will be available in the sent email.00:0002:58
60% Complete -
Ophir Blog
Let’s get started with laser beam profiling
02:57Let’s get started with laser beam profilingWe’d all like it if lasers always worked as they were supposed to – but that’s not always the case. So, like any process, we need some kind of process control – with lasers, you’ll want to be taking accurate measurements.
You might think measuring laser power is enough – but that leaves a lot of the story untold. Instead, laser beam profiling gives you more insight. Let’s explore Ophir’s blog post, and discover how to get started with laser beam profiling.
Let’s imagine a laser as a perfect, idealized beam of light – if something goes wrong, you’ll tweak the power and it will be fixed – right? Unfortunately, it’s not so simple. Lasers degrade with time, and that can change the beam’s spot and shape.
Increasing the beam’s power could even make the shape worse.
Beam profiling is the secret to monitoring laser beam size and shape, to ensure that the beam continues to look and behave exactly as designed.
So, how do you get started in implementing a profiling solution? First, you need to choose the right equipment – and to do that, you need to decide the measurements you’re planning to take. This could include beam width, overall beam shape, ellipticity, and M-squared – the beam quality factor. Most beam parameters are based on these measurements.
Then, it’s time to choose a beam profiler. Most profilers measure beam width – but in different ways. There’s a link in the blog post that explains this further.
Scanning slit profilers take tiny samples of the beam through two narrow slits, creating two one-dimensional profiles on the X-axis and Y-axis. You can use these to create a two dimensional image, but that doesn’t provide a full picture.
CCD cameras can product a full two dimensional image of the laser. But, they require that high power lasers have more attenuation, which can be a hassle. And very small lasers, such as those that are tens of microns, might do better with scanning slits - for higher resolution.
Both scanning slits and CCD cameras can be used to measure ellipticity and M-squared, although M-Squared requires the addition of an optical rail or mirror system to make measurements at multiple locations.
If you’re not sure where to start - visit the blog post and click on the link at the bottom to talk to an Ophir expert.
We just need your phone...After entering the number, the mobile send button will be available to you in all items.
Send to mobileAfter a short one-time registration, all the articles will be opened to you and we will be able to send you the content directly to the mobile (SMS) with a click.We sent you!The option to cancel sending by email and mobile Will be available in the sent email.00:0002:57
60% Complete -
Ophir Blog
The alarming shortage of semiconductor chips
03:01The alarming shortage of semiconductor chipsAs part of a series of blog posts on future trends, Ophir, an MKS company, has raised awareness of an alarming concern – the worldwide shortage of semiconductor chips. These chips are used everywhere – from phones, laptops, and PCs – through to vehicles, washing machines, ATMs, and more.
Let’s find out how this shortage came about, what effects it is having on our world, and see how key players are stepping in to resolve it.
Like many of today’s issues, the trigger behind the semiconductor shortage was the COVID-19 pandemic.
During the pandemic, demand for laptops and computers surged. But this shortage didn’t just affect the production of personal computers, it also had a knock-on effect on other industries.
For example, a new car build typically contains up to 1500 different semiconductor chips. Delivery lead times for chips have gone from an average of 9 weeks, to a staggering 22 weeks.
The result? Delays in the production of over 1 million vehicles in North America alone, with worldwide manufacturers projected to lose about 210 billion dollars in sales.
In China, chip supply chain disruptions caused electricity shortages, leading the government to introduce rationing, ordering factories to work less hours per day. And yes, this has caused Chinese chip manufacturers to reduce their production, creating a catch-22 situation, where the chip shortage is getting harder to resolve.
With these issues creating havoc worldwide, key players have stepped in to assist. Among them - Intel has invested 20 billion dollars in two huge new semiconductor fabrication plants in Arizona.
Samsung Electronics has planned to triple their production capacity by 2026. And TSMC, the largest contract chipmaker in the world, have joined forces with Sony to invest 7 billion dollars in creating a factory in Japan.
Other companies are also ramping up production – SK Hynix, Micron Technology, Bosch, and Hyundai. You can read more about their efforts in the original blog post.
As key suppliers of semiconductor components, MKS also has an important role to play – and is well positioned to support these ongoing industry-wide efforts to increase production.
It’s our hope that with a joint effort, these companies will be able to mitigate the supply chain disruptions that we see today, and get semiconductor production back on track.
We just need your phone...After entering the number, the mobile send button will be available to you in all items.
Send to mobileAfter a short one-time registration, all the articles will be opened to you and we will be able to send you the content directly to the mobile (SMS) with a click.We sent you!The option to cancel sending by email and mobile Will be available in the sent email.00:0003:01
60% Complete -
Ophir Blog
The secret to speedy laser process development
02:51The secret to speedy laser process developmentAnyone involved in automotive manufacturing knows how crucial it is to be able to weld efficiently and accurately. Especially when laser seam welding sheets of zinc-coated steel, a common occurrence in the industry, there are many challenges – as these metals have disparate melting and evaporation properties.
Let’s explore this case study, which shows how Volkswagen’s team of experts in Wolfsburg took on an exciting research project – to develop a new and unique multi-focal laser welding process.
Project leader and engineer Alexander Franz immediately recognized the importance of measurement technologies in laser process development. The time taken to measure a laser has a direct effect on the overall process development time. To speed up development – the team chose Ophir’s BeamWatch laser measurement instrument.
The idea behind multi-focal laser welding is that several laser beams are generated at once by a laser beam optic, to join hot-dip galvanized sheets in a zero-gap configuration. Using two highly focused forward laser beams, and one welding spot, two and three sheet metal joints can be produced with extremely high seam quality.
What the secret to this impressive result? Keeping the geometry of the laser beams completely in sync – and to do that, you need to measure them. You can read the full case study to find out more about the types of measurements taken.
Ophir’s BeamWatch has unique properties which made it suited for this task – it measures the laser beams without touching them, and allows multiple beams to be measured at once.
Each measurement could be taken and displayed in less than 400 milliseconds. This is a massive improvement when compared to the five minutes or more it would take for each measurement, when using other measurement instruments.
In effect, with the BeamWatch, the team was able to see the results of every tiny change they made to the process in real time. Thanks to this – they developed and refined the new welding process very quickly.
Of course, the automotive industry is not the only application the BeamWatch is suited to – it’s compact, flexible, and easy to set up – making it ideal for troubleshooting and laser process development in any field.
We just need your phone...After entering the number, the mobile send button will be available to you in all items.
Send to mobileAfter a short one-time registration, all the articles will be opened to you and we will be able to send you the content directly to the mobile (SMS) with a click.We sent you!The option to cancel sending by email and mobile Will be available in the sent email.00:0002:51
60% Complete -
Ophir Blog
How we found the right beam profiling solution for a nuclear-powered US Army submarine
02:42How we found the right beam profiling solution for a nuclear-powered US Army submarinehttp://summur.ai/lFYVYHow we found the right beam profiling solution for a nuclear-powered US Army submarineHow we found the right beam profiling solution for a nuclear-powered US Army submarine
This case study follows the journey of the Ophir team, as they worked tirelessly to find the right beam profiling solution for a nuclear-powered submarine.
You’ll find out the winning combination of technologies, tools, and techniques that were used to carry out this challenging task.
The US Army embraces emerging technologies – and so, the Ophir team ended up looking into laser measurements for a laser in the periscope of a 6800 ton, nuclear-powered submarine.Of course, as with any military application, there are strict requirements to meet. In this case, the laser had to be extremely accurate.
As you can imagine, there are few things more challenging than ensuring high laser accuracy on a moving, underwater vehicle.
This laser operates in conditions with limited inputs - GPS data, and the influence of gravity on its orientation and alignment.
As a result, the quality of the laser beam - and its shape, size, and intensity - all become critical - and beam alignment must be measured with extremely high accuracy.Finding the right instrumentation for these measurements wasn’t easy!
After several attempts, the Ophir team discovered a winning combination - Ophir-Spiricon BeamGage software, together with the Spiricon SP300 - a high-speed, high-resolution USB3 CCD camera.
Three key measurements were taken - a baseline source beam measurement, the beam’s ellipticity, and the laser source’s Gaussian Fit.
Next, these measurements were repeated at greater distances from the source, to calculate changes, and see if these changes were within tolerance. This method allowed them to capture both qualitative and quantitative differences, so the source could be improved and adjusted.
The beam profiling software proved itself vital for capturing the measurements and images needed. This data was used to identify the critical variables, from both the laser source and the final assembly, which would have an impact on the system.
With the right technologies, techniques, and tools - the team was able to ensure maximum laser system performance for this challenging underwater military application.
Take a look at the original case study – where you’ll see some of the measurements captured, in their graphical form.
Dick RieleyEast Coast Regional Sales Manager, Ophir Photonics GroupWe just need your phone...After entering the number, the mobile send button will be available to you in all items.
Send to mobileAfter a short one-time registration, all the articles will be opened to you and we will be able to send you the content directly to the mobile (SMS) with a click.We sent you!The option to cancel sending by email and mobile Will be available in the sent email.00:0002:42
60% Complete

We’d love to hear your thoughts.
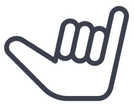
We are happy to learn and improve for you.